Intro
Boost system efficiency by testing points condenser effectiveness, optimizing heat transfer, and enhancing refrigeration cycles with key performance indicators and diagnostic tools.
The concept of condensation is a fundamental principle in physics and chemistry, and its application is vast and varied. Condensers are devices that utilize this principle to transfer heat from one medium to another, often with the goal of cooling or condensing a substance. In various industries, including power generation, refrigeration, and chemical processing, condensers play a critical role. Understanding the effectiveness of condensers is essential for optimizing their performance, reducing energy consumption, and enhancing overall system efficiency.
The effectiveness of a condenser is determined by its ability to transfer heat efficiently, which is influenced by several factors, including the design of the condenser, the materials used, and the operating conditions. A well-designed condenser can significantly improve the overall efficiency of a system, leading to cost savings and reduced environmental impact. Conversely, a poorly designed or malfunctioning condenser can lead to decreased system performance, increased energy consumption, and potential safety hazards.
In the context of testing points condenser effectiveness, it is crucial to consider the various parameters that affect condenser performance. These parameters include the heat transfer coefficient, the condenser's surface area, the flow rates of the fluids involved, and the temperature differences between the hot and cold sides of the condenser. By analyzing these parameters and their interactions, engineers and technicians can identify areas for improvement and optimize condenser design and operation for maximum effectiveness.
Introduction to Condensers
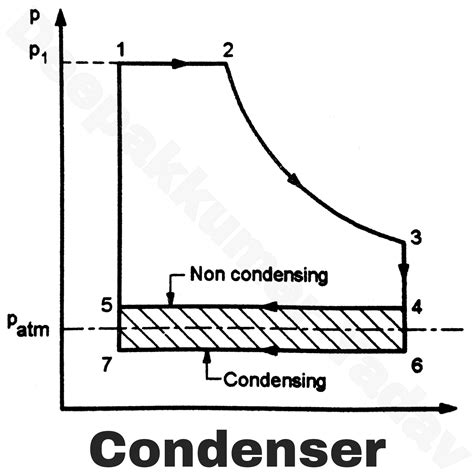
Condensers are widely used in various applications, including power plants, refrigeration systems, and chemical plants. They operate by transferring heat from a hot fluid to a cooler fluid, causing the hot fluid to condense. This process is essential for efficient heat transfer and is critical in many industrial processes. Condensers can be classified into different types, including shell and tube condensers, plate condensers, and evaporative condensers, each with its unique design and operating characteristics.
Types of Condensers
The choice of condenser type depends on the specific application, the fluids involved, and the operating conditions. Shell and tube condensers, for example, are commonly used in power plants and chemical processing due to their high heat transfer coefficients and robust design. Plate condensers, on the other hand, are often used in refrigeration systems and air conditioning units due to their compact design and high efficiency. Evaporative condensers, which utilize the evaporation of water to cool the hot fluid, are frequently used in applications where water is readily available and the cooling requirements are moderate.Factors Affecting Condenser Effectiveness
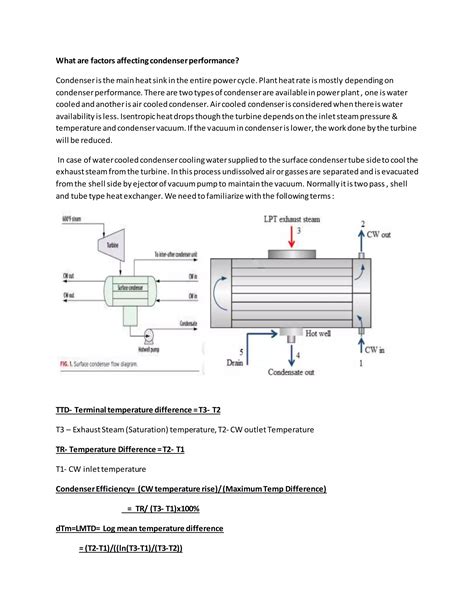
Several factors can influence the effectiveness of a condenser, including the design parameters, the materials used, and the operating conditions. The heat transfer coefficient, which is a measure of the condenser's ability to transfer heat, is a critical factor. A higher heat transfer coefficient indicates more efficient heat transfer and, consequently, better condenser performance. The surface area of the condenser, the flow rates of the fluids, and the temperature differences between the hot and cold sides also play significant roles in determining condenser effectiveness.
Design Parameters
The design of a condenser is crucial for its effectiveness. The surface area, the arrangement of the tubes or plates, and the materials used can all impact the heat transfer coefficient and the overall performance of the condenser. For instance, a condenser with a larger surface area can provide more efficient heat transfer, but it may also increase the cost and the space requirements. Similarly, the choice of materials can affect the durability and the maintenance requirements of the condenser.Testing and Evaluation of Condenser Effectiveness
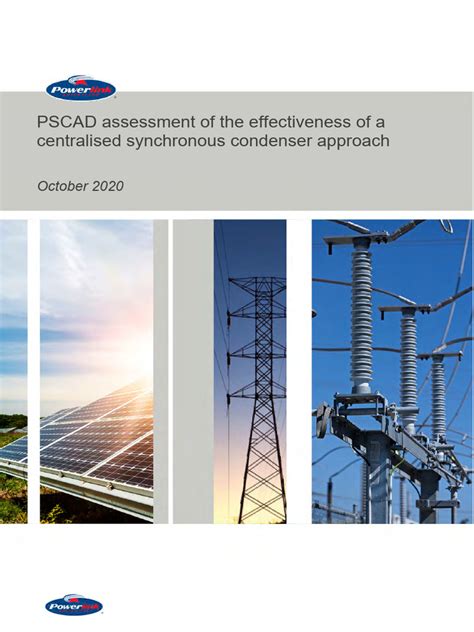
Evaluating the effectiveness of a condenser involves measuring its heat transfer performance under various operating conditions. This can be achieved through experiments, simulations, or a combination of both. The heat transfer coefficient, the condensation rate, and the pressure drop across the condenser are key parameters that need to be measured or calculated. By analyzing these parameters, engineers can identify potential issues, optimize the design, and improve the overall efficiency of the condenser.
Experimental Methods
Experimental methods involve conducting tests on the condenser under controlled conditions to measure its performance. This can include measuring the temperature differences, the flow rates, and the pressure drops across the condenser. The data collected from these experiments can be used to calculate the heat transfer coefficient and the condensation rate, providing valuable insights into the condenser's effectiveness.Optimization of Condenser Design
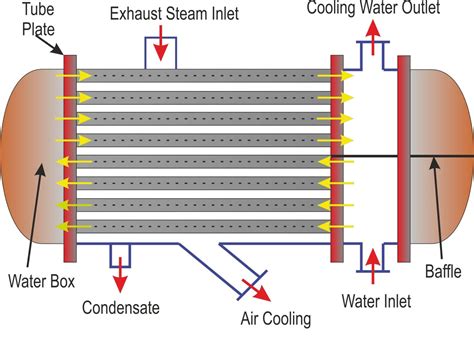
Optimizing the design of a condenser involves modifying its parameters to achieve the best possible performance. This can include adjusting the surface area, the tube or plate arrangement, and the materials used. Computational models and simulation tools can be employed to predict the performance of different design configurations, allowing for the identification of the most effective design without the need for physical prototypes.
Computational Models
Computational models, such as finite element analysis and computational fluid dynamics, can simulate the heat transfer and fluid flow within a condenser. These models can predict the performance of the condenser under various operating conditions, enabling the optimization of its design. By iterating through different design scenarios and analyzing the simulated performance, engineers can converge on an optimal design that maximizes the condenser's effectiveness.Applications and Future Directions
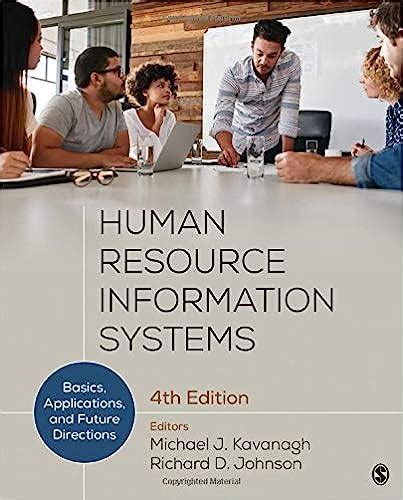
Condensers have a wide range of applications across various industries, from power generation and refrigeration to chemical processing and air conditioning. As technology advances and the demand for more efficient and sustainable systems grows, the development of more effective condensers will play a critical role. Future directions may include the use of advanced materials, innovative designs, and integrated systems that combine multiple functions, such as heat transfer and mass transfer.
Sustainability and Efficiency
The push for sustainability and efficiency is driving the development of condensers that can operate with minimal environmental impact. This includes the use of eco-friendly refrigerants, the optimization of energy consumption, and the reduction of waste heat. By focusing on these aspects, the design and operation of condensers can be significantly improved, contributing to a more sustainable future.Condenser Image Gallery
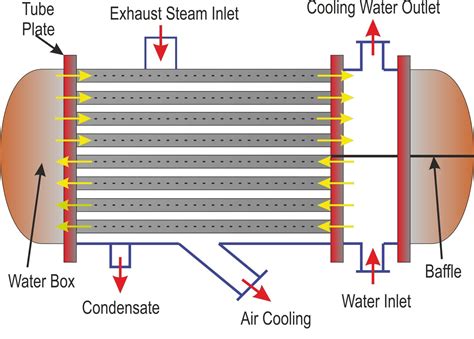
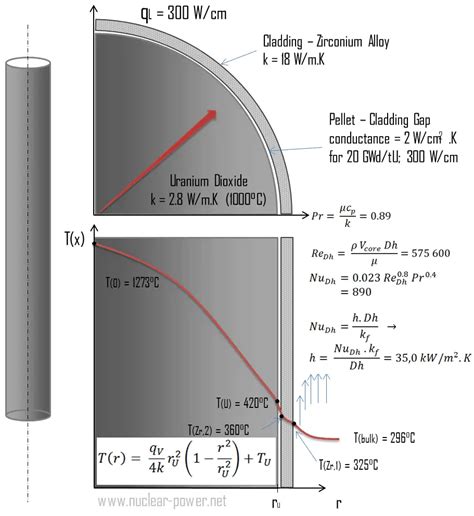
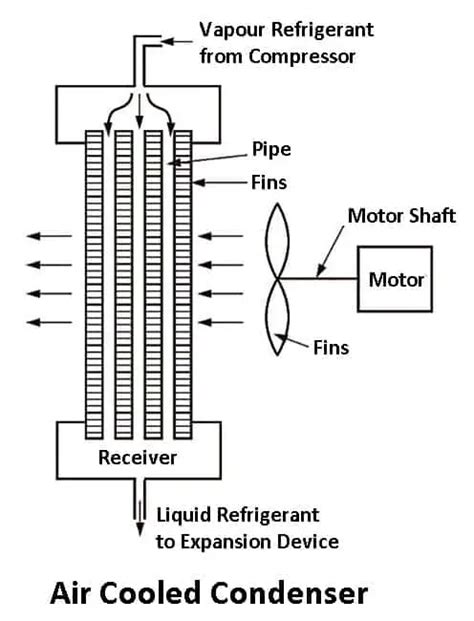
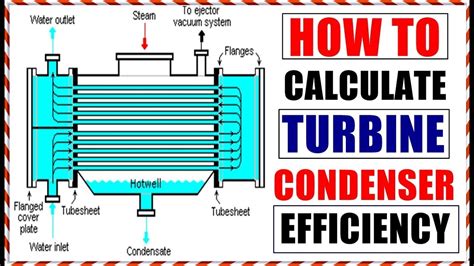
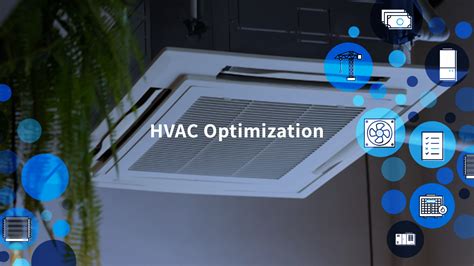
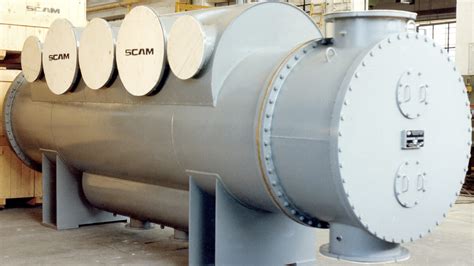
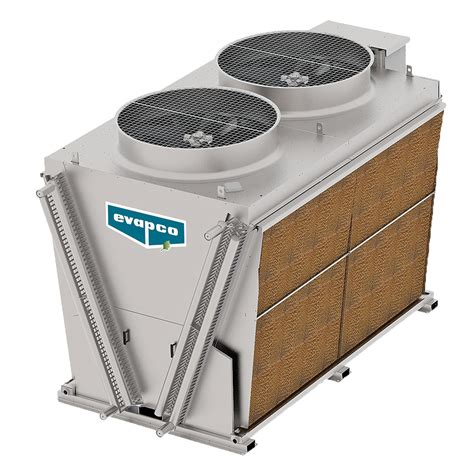
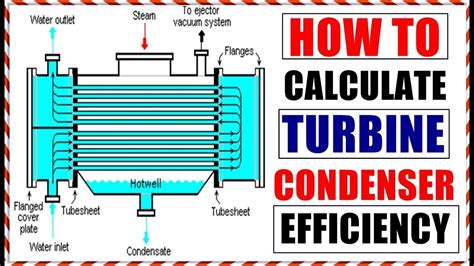
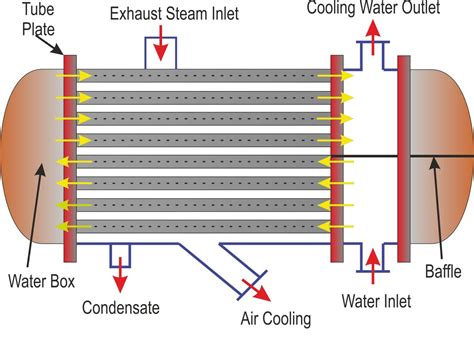
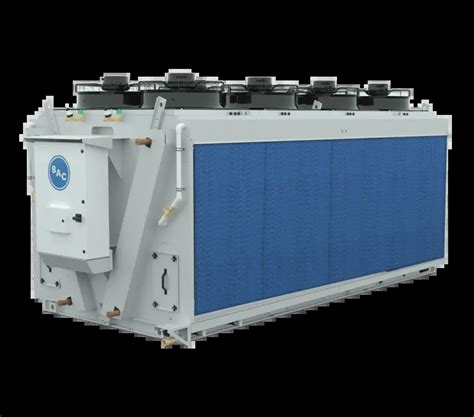
What is the primary function of a condenser?
+The primary function of a condenser is to transfer heat from a hot fluid to a cooler fluid, causing the hot fluid to condense.
What factors affect the effectiveness of a condenser?
+The effectiveness of a condenser is affected by several factors, including the heat transfer coefficient, the surface area, the flow rates of the fluids, and the temperature differences between the hot and cold sides.
How can the design of a condenser be optimized?
+The design of a condenser can be optimized by modifying its parameters, such as the surface area, the tube or plate arrangement, and the materials used, to achieve the best possible performance. Computational models and simulation tools can be employed to predict the performance of different design configurations.
In summary, understanding the effectiveness of condensers and how to optimize their design is crucial for improving the efficiency and sustainability of various industrial processes. By considering the factors that affect condenser performance, utilizing computational models for design optimization, and focusing on innovative technologies and materials, significant advancements can be made in condenser technology. As the demand for more efficient and environmentally friendly systems continues to grow, the development of advanced condensers will play a vital role in meeting these challenges. We invite readers to share their thoughts and experiences on condenser effectiveness and optimization, and we look forward to exploring new directions in condenser technology together.