Intro
Master Mig welding techniques for strong, precise joints. Learn effective welder settings, metal preparation, and safety tips for Gas Metal Arc Welding, improving your GMAW skills and projects.
Mig welding, also known as Gas Metal Arc Welding (GMAW), is a popular welding process used in various industries, including construction, automotive, and manufacturing. It is a versatile and efficient method for joining metal pieces together, offering high-quality welds with minimal distortion. However, to achieve optimal results, it is essential to use mig welding effectively. In this article, we will explore the importance of mig welding, its benefits, and provide tips on how to use it effectively.
Mig welding has become a widely accepted technique in the welding industry due to its simplicity, speed, and cost-effectiveness. It involves the use of a continuous wire feed, which is melted and deposited onto the workpiece, creating a strong and durable bond. The process is relatively easy to learn, and with practice, welders can achieve high-quality results. Moreover, mig welding can be used on a variety of metals, including steel, aluminum, and stainless steel, making it a versatile technique for various applications.
The effectiveness of mig welding depends on several factors, including the welder's skill level, equipment quality, and technique. To achieve optimal results, welders must understand the fundamentals of mig welding, including the proper setup of equipment, selection of welding parameters, and technique. Additionally, welders must be aware of the potential hazards associated with mig welding, such as electrical shock, fire, and exposure to fumes and radiation. By following safety guidelines and using proper techniques, welders can minimize risks and produce high-quality welds.
Understanding Mig Welding Equipment
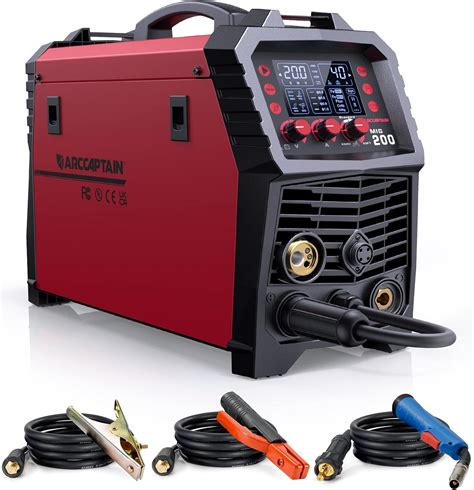
To use mig welding effectively, it is essential to understand the equipment involved. A typical mig welding setup consists of a welding machine, wire feed system, torch, and shielding gas. The welding machine provides the electrical power necessary for the welding process, while the wire feed system delivers the wire to the torch. The torch is used to direct the wire to the workpiece, and the shielding gas protects the weld area from atmospheric gases. Understanding how each component functions and interacts with others is crucial for achieving optimal results.
Setting Up Mig Welding Equipment
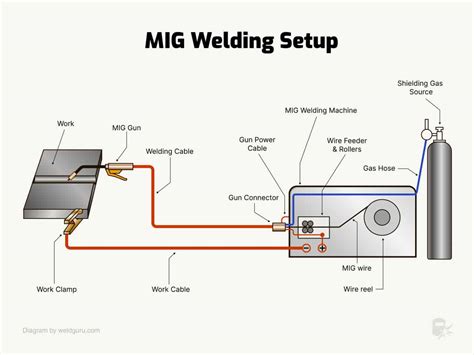
Setting up mig welding equipment requires attention to detail and a thorough understanding of the process. The first step is to select the correct welding parameters, including voltage, current, and wire feed speed. The welding machine should be set to the recommended parameters for the specific metal being welded. Next, the wire feed system should be adjusted to ensure a consistent wire feed rate. The torch should be properly connected to the welding machine and wire feed system, and the shielding gas should be turned on. Finally, the workpiece should be properly prepared, including cleaning and removing any debris or oxidation.
Mig Welding Techniques
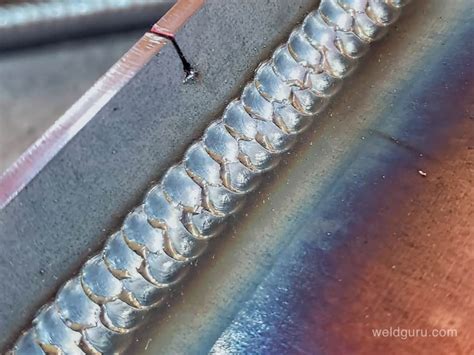
Mig welding techniques play a crucial role in achieving high-quality welds. The most common technique used in mig welding is the push technique, where the torch is pushed away from the weld pool. This technique is used for most welding applications and provides a smooth, consistent weld. Another technique used is the pull technique, where the torch is pulled towards the weld pool. This technique is used for welding thinner metals and provides a more controlled weld. Additionally, welders can use various welding patterns, such as the zig-zag or circular pattern, to achieve specific weld characteristics.
Benefits of Mig Welding
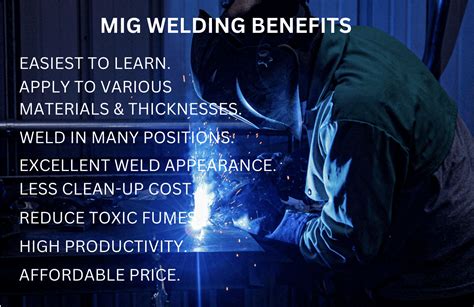
Mig welding offers several benefits, including high-quality welds, increased productivity, and cost-effectiveness. The process is relatively fast, allowing welders to complete projects quickly and efficiently. Additionally, mig welding can be used on a variety of metals, making it a versatile technique for various applications. The process also provides a clean and smooth weld, reducing the need for post-weld cleaning and finishing. Furthermore, mig welding is a relatively safe process, with minimal risks of electrical shock, fire, and exposure to fumes and radiation.
Common Mistakes in Mig Welding
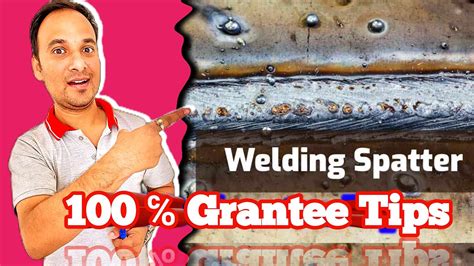
Despite its simplicity, mig welding can be prone to errors, especially for inexperienced welders. One common mistake is incorrect welding parameters, which can result in poor weld quality or lack of penetration. Another mistake is inadequate shielding gas, which can lead to porosity or lack of fusion. Additionally, welders may experience difficulties with wire feed, such as bird-nesting or wire tangling, which can disrupt the welding process. To avoid these mistakes, welders should follow proper setup and technique guidelines, and regularly inspect their equipment and welds.
Applications of Mig Welding
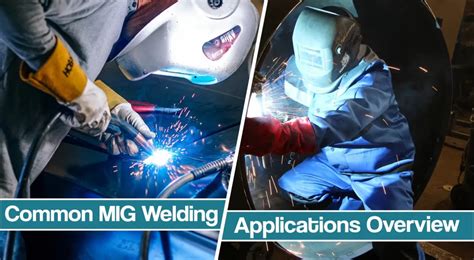
Mig welding has a wide range of applications, including construction, automotive, and manufacturing. The process is commonly used for welding steel, aluminum, and stainless steel, making it a versatile technique for various industries. In construction, mig welding is used for building frameworks, bridges, and other structural components. In the automotive industry, mig welding is used for manufacturing vehicle components, such as chassis, engines, and exhaust systems. Additionally, mig welding is used in manufacturing for producing equipment, machinery, and other metal products.
Training and Certification
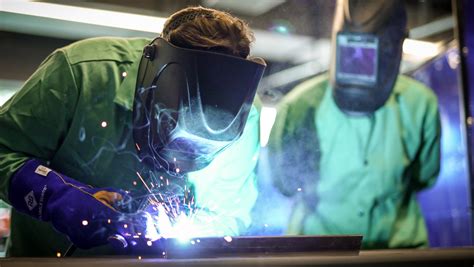
To become a skilled mig welder, it is essential to undergo proper training and certification. Welding training programs are available at vocational schools, community colleges, and welding institutes. These programs provide hands-on training and instruction on mig welding techniques, safety procedures, and equipment operation. Additionally, welders can obtain certification from organizations, such as the American Welding Society (AWS) or the American Society of Mechanical Engineers (ASME). Certification demonstrates a welder's competence and expertise in mig welding, making them more attractive to potential employers.
Gallery of Mig Welding
Mig Welding Image Gallery
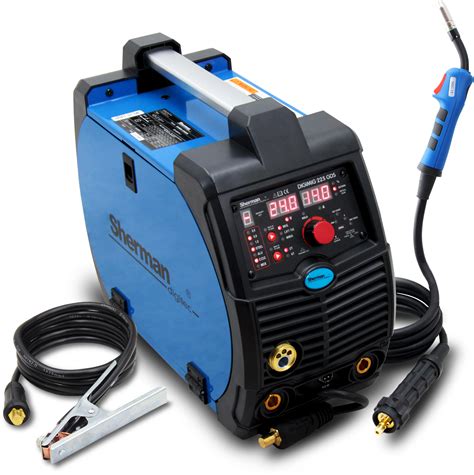
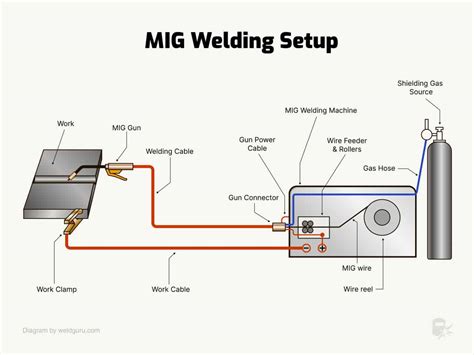
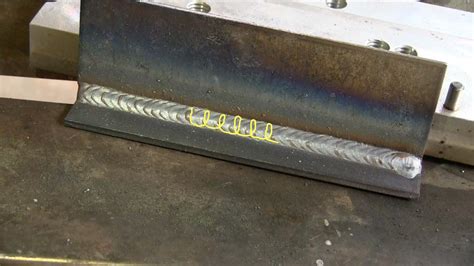
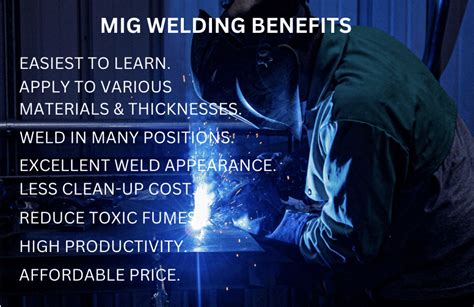
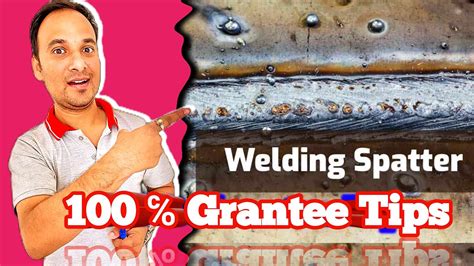
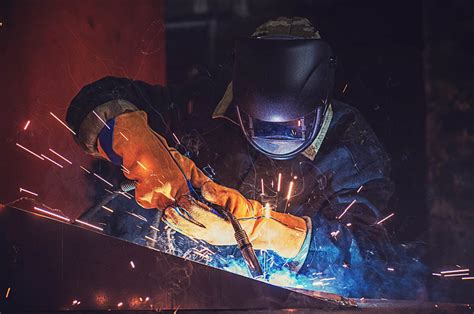
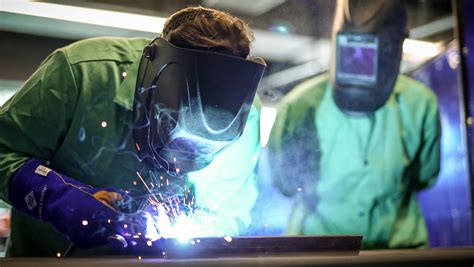
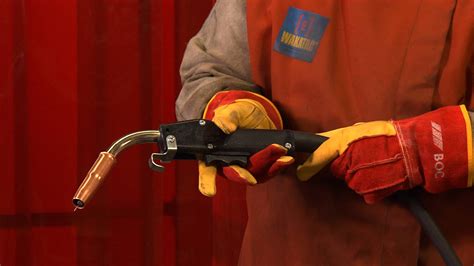
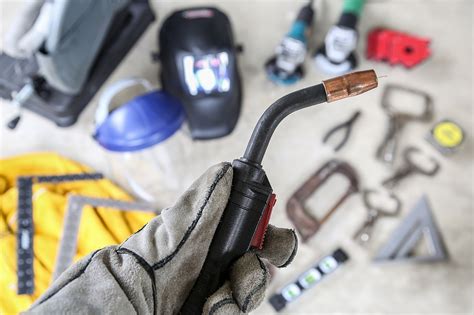
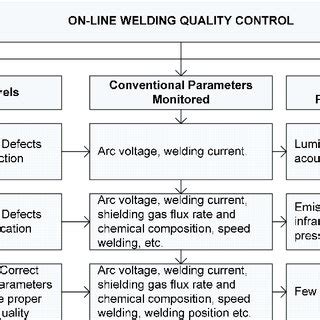
What is mig welding?
+Mig welding, also known as Gas Metal Arc Welding (GMAW), is a popular welding process used in various industries, including construction, automotive, and manufacturing.
What are the benefits of mig welding?
+Mig welding offers several benefits, including high-quality welds, increased productivity, and cost-effectiveness. The process is relatively fast, allowing welders to complete projects quickly and efficiently.
What are the common mistakes in mig welding?
+Common mistakes in mig welding include incorrect welding parameters, inadequate shielding gas, and difficulties with wire feed. To avoid these mistakes, welders should follow proper setup and technique guidelines, and regularly inspect their equipment and welds.
What is the importance of training and certification in mig welding?
+To become a skilled mig welder, it is essential to undergo proper training and certification. Welding training programs provide hands-on training and instruction on mig welding techniques, safety procedures, and equipment operation. Certification demonstrates a welder's competence and expertise in mig welding, making them more attractive to potential employers.
What are the applications of mig welding?
+Mig welding has a wide range of applications, including construction, automotive, and manufacturing. The process is commonly used for welding steel, aluminum, and stainless steel, making it a versatile technique for various industries.
In conclusion, mig welding is a versatile and efficient welding process used in various industries. To use mig welding effectively, it is essential to understand the equipment, setup, and techniques involved. By following proper guidelines and safety procedures, welders can achieve high-quality welds and minimize risks. With its numerous benefits, including increased productivity and cost-effectiveness, mig welding is an ideal technique for various applications. Whether you are a beginner or an experienced welder, understanding the fundamentals of mig welding can help you improve your skills and produce high-quality welds. We encourage you to share your experiences and tips on using mig welding effectively, and to ask any questions you may have about this versatile welding process.