Intro
Discover the impact of faulty welds at Newport News Shipyard, affecting shipbuilding quality, safety, and repair costs, with issues like welding defects, inspection failures, and naval contract implications.
The importance of ensuring the quality and integrity of welds in shipbuilding cannot be overstated. A single faulty weld can compromise the entire structure of a vessel, posing significant risks to the safety of its crew, passengers, and cargo. Recently, concerns have been raised about the presence of faulty welds at the Newport News Shipyard, a major shipbuilding facility in the United States. This issue has sparked a heated debate about the need for more stringent quality control measures in the shipbuilding industry.
The discovery of faulty welds at the Newport News Shipyard has significant implications for the safety and reliability of the vessels constructed at this facility. Welding is a critical process in shipbuilding, as it is used to join together the various components of a vessel's hull and superstructure. If a weld is faulty, it can create a weak point in the structure of the vessel, making it more susceptible to damage from stress, fatigue, and other external factors. This, in turn, can increase the risk of accidents, injuries, and even fatalities.
The presence of faulty welds at the Newport News Shipyard is not an isolated incident, but rather a symptom of a broader problem in the shipbuilding industry. The pressure to meet tight production schedules and budgets can sometimes lead to shortcuts and compromises on quality, which can have serious consequences. Furthermore, the complexity of modern shipbuilding projects, which often involve the use of advanced materials and technologies, can make it more challenging to ensure the quality and integrity of welds.
Introduction to Welding in Shipbuilding
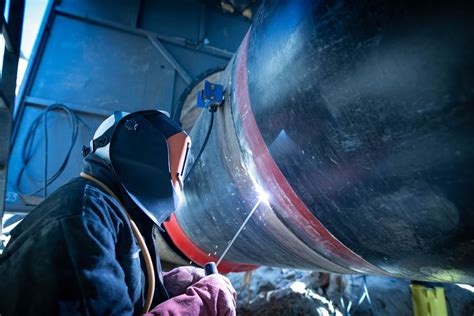
Types of Welding Used in Shipbuilding
There are several types of welding used in shipbuilding, including shielded metal arc welding (SMAW), gas metal arc welding (GMAW), and gas tungsten arc welding (GTAW). Each type of welding has its own advantages and disadvantages, and the choice of welding process depends on the specific requirements of the project. SMAW is a commonly used welding process in shipbuilding, as it is relatively simple and inexpensive. However, it can be time-consuming and may not be suitable for welding thin materials. GMAW and GTAW are more advanced welding processes that offer higher speeds and better quality, but they require more specialized equipment and training.Causes of Faulty Welds
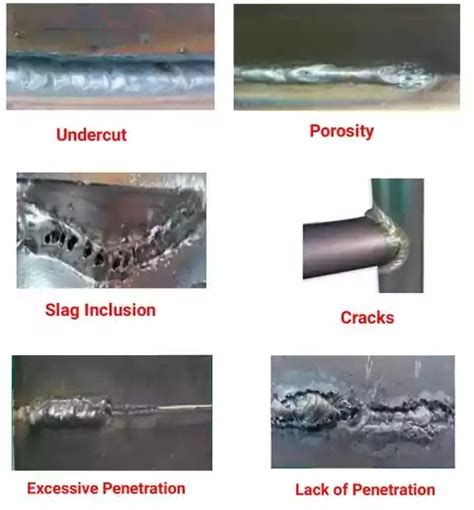
Consequences of Faulty Welds
The consequences of faulty welds can be severe, ranging from minor repairs to major accidents and fatalities. Faulty welds can compromise the structural integrity of a vessel, making it more susceptible to damage from stress, fatigue, and other external factors. This can lead to a range of problems, including leaks, cracks, and even catastrophic failures. Furthermore, faulty welds can also lead to costly repairs and maintenance, as well as downtime and lost productivity.Quality Control Measures
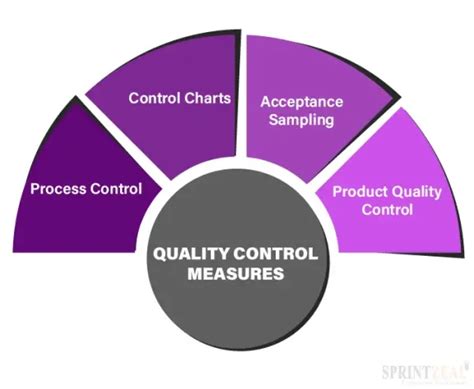
Best Practices for Welding in Shipbuilding
There are several best practices that can be implemented to ensure high-quality welds in shipbuilding. These include the use of proper welding techniques, regular equipment maintenance, and adequate quality control measures. Proper welding techniques include the use of correct welding parameters, such as voltage, current, and travel speed, as well as the use of proper welding consumables, such as electrodes and shielding gas. Regular equipment maintenance is also essential, as malfunctioning equipment can produce inconsistent and low-quality welds.Regulatory Framework
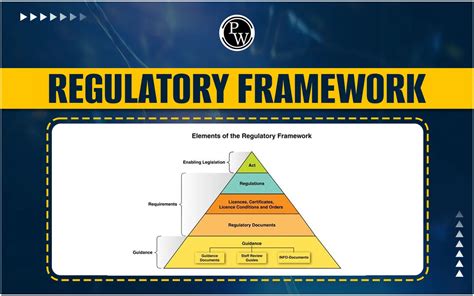
Industry Standards and Certifications
There are several industry standards and certifications that are relevant to welding in shipbuilding. These include the American Society of Mechanical Engineers (ASME) Boiler and Pressure Vessel Code, as well as the American Welding Society (AWS) Certification Program. The ASME Code provides guidelines for the design, fabrication, and inspection of boilers and pressure vessels, while the AWS Certification Program provides a framework for certifying welders and welding inspectors.Welding in Shipbuilding Image Gallery
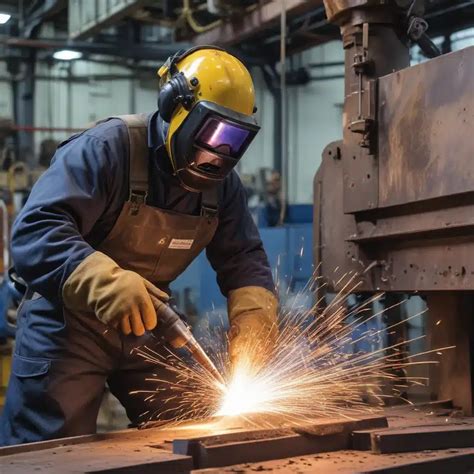
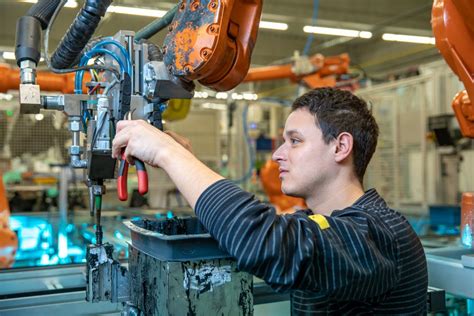

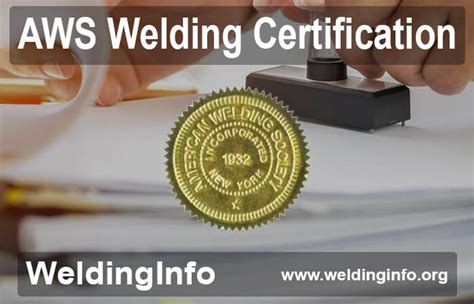
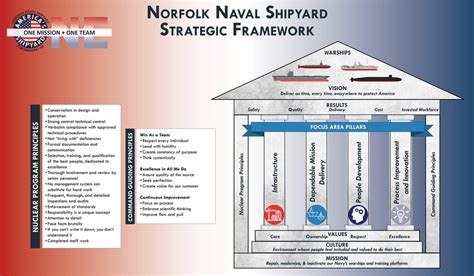
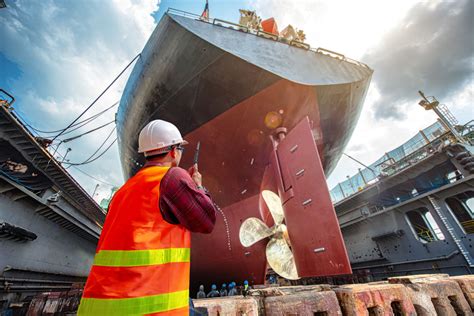

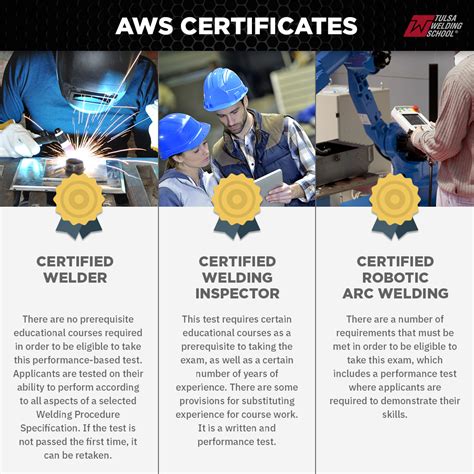
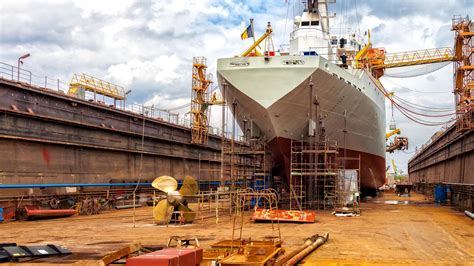
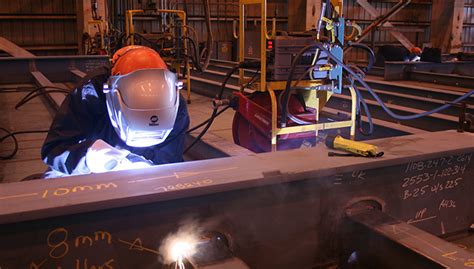
What are the causes of faulty welds in shipbuilding?
+Faulty welds can occur due to a variety of reasons, including inadequate training, poor equipment maintenance, and insufficient quality control measures.
What are the consequences of faulty welds in shipbuilding?
+The consequences of faulty welds can be severe, ranging from minor repairs to major accidents and fatalities.
What are the best practices for welding in shipbuilding?
+Best practices for welding in shipbuilding include the use of proper welding techniques, regular equipment maintenance, and adequate quality control measures.
In conclusion, the presence of faulty welds at the Newport News Shipyard highlights the need for more stringent quality control measures in the shipbuilding industry. Ensuring the quality and integrity of welds is critical to the safety and reliability of vessels, and it requires a combination of proper training, equipment maintenance, and quality control measures. By implementing effective quality control measures and best practices, the shipbuilding industry can minimize the risk of faulty welds and ensure the safety and quality of vessels. We invite our readers to share their thoughts and experiences on this topic, and we hope that this article has provided valuable insights into the importance of welding in shipbuilding.