Intro
Discover what MIG stands for in welding, including Metal Inert Gas process, equipment, and techniques, for improved shielding gas, arc stability, and weld quality.
MIG stands for Metal Inert Gas, which is a type of welding process that uses a continuous wire feed and an inert gas to shield the weld area from atmospheric gases. This process is also known as Gas Metal Arc Welding (GMAW). The MIG welding process is widely used in various industries, including construction, automotive, and manufacturing, due to its high speed, efficiency, and versatility.
The MIG welding process involves the use of a welding gun, which feeds a continuous wire electrode into the weld area. The wire is surrounded by an inert gas, such as argon or helium, which protects the weld from atmospheric gases and prevents porosity and oxidation. The welding gun is connected to a power source, which provides the electrical current necessary for the welding process.
MIG welding is a popular choice for many applications because it offers several advantages over other welding processes. Some of the benefits of MIG welding include high speed, low distortion, and good penetration. Additionally, MIG welding can be used to weld a wide range of metals, including steel, aluminum, and stainless steel.
Introduction to MIG Welding
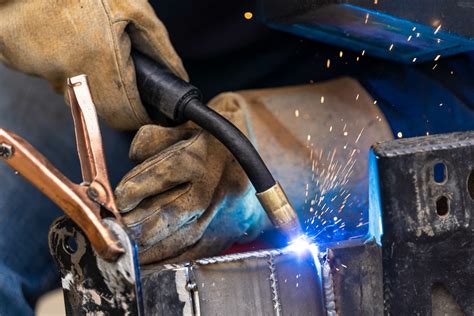
The MIG welding process is relatively easy to learn, and it can be used for a variety of applications, including repair work, fabrication, and construction. However, it does require some practice and patience to master the technique. With the right equipment and training, anyone can learn to use the MIG welding process to create high-quality welds.
How MIG Welding Works
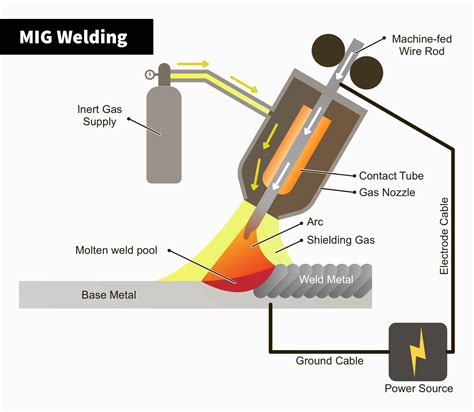
The MIG welding process involves several key components, including the welding gun, wire feed system, and power source. The welding gun is used to feed the wire electrode into the weld area, while the wire feed system controls the rate at which the wire is fed. The power source provides the electrical current necessary for the welding process.
Key Components of MIG Welding
The key components of the MIG welding process include: * Welding gun: This is the device used to feed the wire electrode into the weld area. * Wire feed system: This system controls the rate at which the wire is fed into the weld area. * Power source: This provides the electrical current necessary for the welding process. * Inert gas: This is used to shield the weld area from atmospheric gases and prevent porosity and oxidation.Benefits of MIG Welding
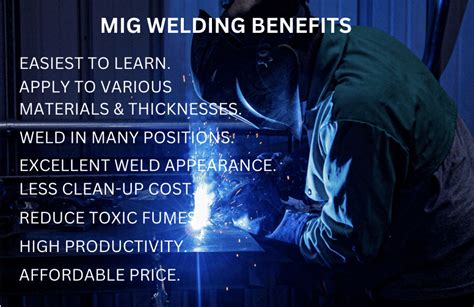
MIG welding offers several benefits, including high speed, low distortion, and good penetration. Additionally, MIG welding can be used to weld a wide range of metals, including steel, aluminum, and stainless steel. The process is also relatively easy to learn, and it can be used for a variety of applications, including repair work, fabrication, and construction.
Advantages of MIG Welding
Some of the advantages of MIG welding include: * High speed: MIG welding is a fast process, which makes it ideal for large-scale production and repair work. * Low distortion: MIG welding produces minimal distortion, which makes it ideal for applications where precision is critical. * Good penetration: MIG welding provides good penetration, which makes it ideal for applications where thick metals need to be welded. * Versatility: MIG welding can be used to weld a wide range of metals, including steel, aluminum, and stainless steel.MIG Welding Applications
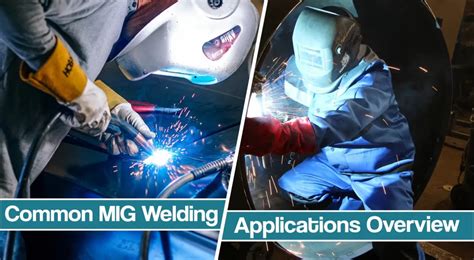
MIG welding has a wide range of applications, including repair work, fabrication, and construction. The process is commonly used in the automotive, construction, and manufacturing industries. Additionally, MIG welding can be used for DIY projects and hobbyist activities.
Common Applications of MIG Welding
Some of the common applications of MIG welding include: * Repair work: MIG welding is often used for repair work, such as fixing broken equipment and machinery. * Fabrication: MIG welding is used for fabrication, such as building frames and structures. * Construction: MIG welding is used in construction, such as building bridges and buildings. * Automotive: MIG welding is used in the automotive industry, such as repairing and manufacturing vehicle parts.MIG Welding Equipment
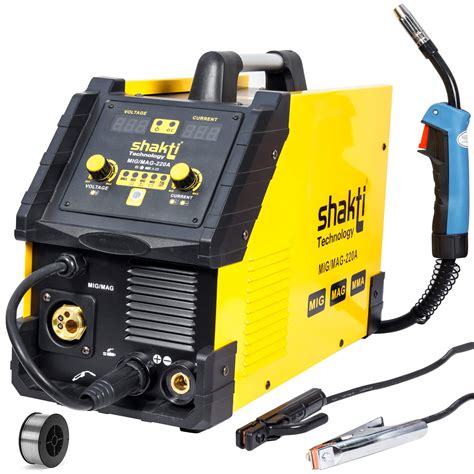
MIG welding equipment includes the welding gun, wire feed system, and power source. The welding gun is used to feed the wire electrode into the weld area, while the wire feed system controls the rate at which the wire is fed. The power source provides the electrical current necessary for the welding process.
Types of MIG Welding Equipment
Some of the types of MIG welding equipment include: * Welding gun: This is the device used to feed the wire electrode into the weld area. * Wire feed system: This system controls the rate at which the wire is fed into the weld area. * Power source: This provides the electrical current necessary for the welding process. * Inert gas: This is used to shield the weld area from atmospheric gases and prevent porosity and oxidation.MIG Welding Safety
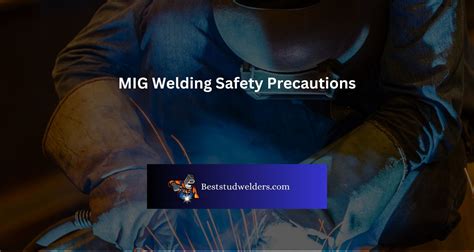
MIG welding safety is critical to prevent injuries and ensure a safe working environment. Some of the safety precautions include wearing protective gear, such as gloves and a welding helmet, and ensuring good ventilation in the work area.
Safety Precautions for MIG Welding
Some of the safety precautions for MIG welding include: * Wearing protective gear: This includes gloves, a welding helmet, and safety glasses. * Ensuring good ventilation: This is critical to prevent inhalation of fumes and particles. * Keeping the work area clean: This is critical to prevent accidents and ensure a safe working environment.MIG Welding Image Gallery
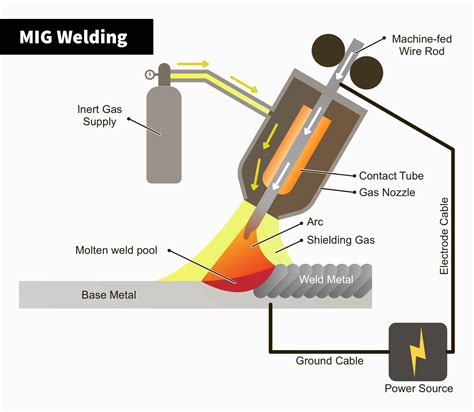
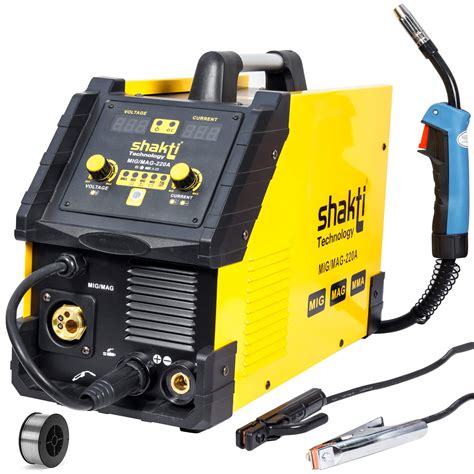
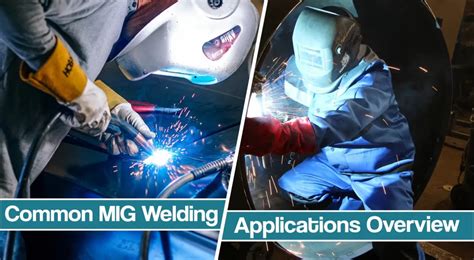
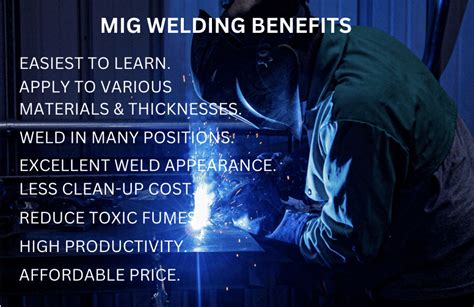
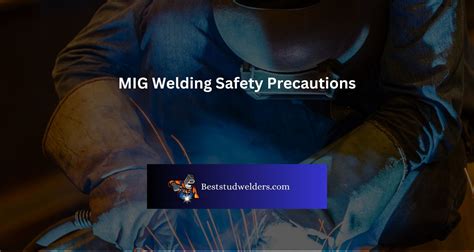
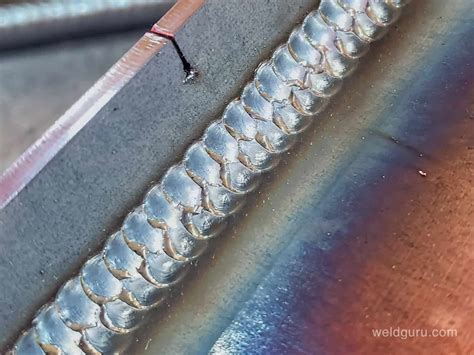
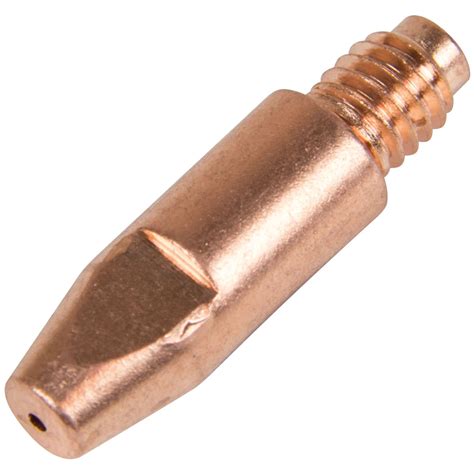
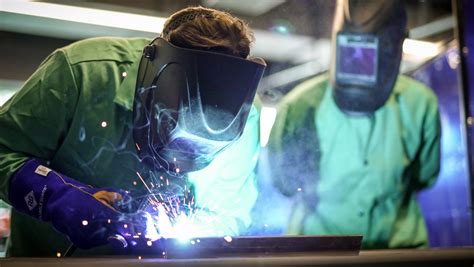
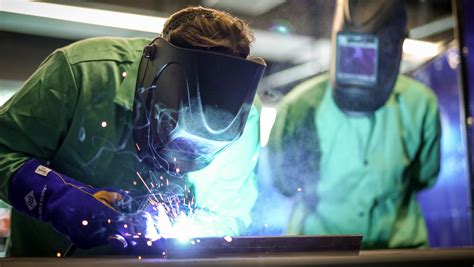
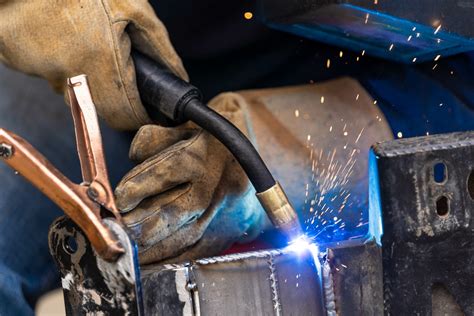
What is MIG welding?
+MIG welding is a type of welding process that uses a continuous wire feed and an inert gas to shield the weld area from atmospheric gases.
What are the benefits of MIG welding?
+MIG welding offers several benefits, including high speed, low distortion, and good penetration. Additionally, MIG welding can be used to weld a wide range of metals, including steel, aluminum, and stainless steel.
What are the common applications of MIG welding?
+MIG welding has a wide range of applications, including repair work, fabrication, and construction. The process is commonly used in the automotive, construction, and manufacturing industries.
What safety precautions should be taken when MIG welding?
+MIG welding safety is critical to prevent injuries and ensure a safe working environment. Some of the safety precautions include wearing protective gear, such as gloves and a welding helmet, and ensuring good ventilation in the work area.
What equipment is needed for MIG welding?
+MIG welding equipment includes the welding gun, wire feed system, and power source. The welding gun is used to feed the wire electrode into the weld area, while the wire feed system controls the rate at which the wire is fed. The power source provides the electrical current necessary for the welding process.
We hope this article has provided you with a comprehensive understanding of MIG welding and its applications. Whether you are a beginner or an experienced welder, MIG welding is a valuable skill to have in your toolkit. With its high speed, low distortion, and good penetration, MIG welding is an ideal process for a wide range of applications. If you have any questions or comments, please feel free to share them below. Additionally, if you found this article helpful, please share it with your friends and colleagues who may be interested in learning more about MIG welding.