Intro
Navy shipyard welding issues arise from poor technique, corrosion, and metal fatigue, affecting vessel integrity and safety, highlighting need for advanced welding methods and quality control measures.
The importance of maintaining and repairing naval ships cannot be overstated, as these vessels play a critical role in national defense and security. One of the key aspects of ship maintenance is welding, which is used to join and repair various components of the ship's structure. However, welding in a navy shipyard can be a complex and challenging process, with several issues that can affect the quality and safety of the repairs. In this article, we will explore some of the common welding issues that can arise in a navy shipyard and discuss ways to mitigate them.
Welding is a critical process in ship repair, as it is used to join steel plates, pipes, and other components that make up the ship's hull and superstructure. The quality of the welds is crucial, as they must be able to withstand the stresses and strains of the marine environment, including waves, tides, and extreme weather conditions. Any defects or weaknesses in the welds can compromise the safety of the ship and its crew, making it essential to identify and address any welding issues promptly.
The welding process in a navy shipyard involves several stages, including preparation, welding, and inspection. The preparation stage involves cleaning and preparing the surfaces to be welded, as well as selecting the appropriate welding procedure and materials. The welding stage involves joining the components using a welding torch or other equipment, while the inspection stage involves checking the welds for defects or weaknesses. Each stage of the process requires careful attention to detail and a high level of skill and expertise, as any mistakes or errors can have serious consequences.
Common Welding Issues in Navy Shipyard
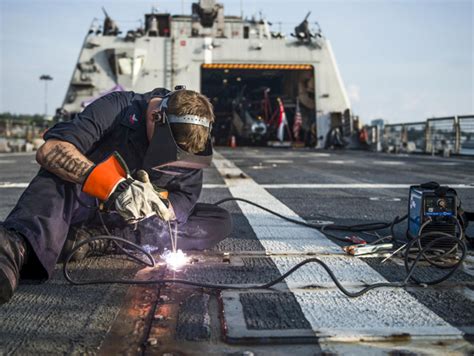
Some of the common welding issues that can arise in a navy shipyard include porosity, lack of fusion, and cracking. Porosity refers to the presence of small holes or voids in the weld, which can weaken the joint and make it more susceptible to corrosion. Lack of fusion occurs when the weld metal does not fully penetrate the base metal, resulting in a weak bond between the two. Cracking can occur due to thermal stresses, poor welding technique, or the use of incorrect welding materials. These issues can be caused by a variety of factors, including inadequate training, poor equipment maintenance, and insufficient quality control measures.
Causes of Welding Issues
The causes of welding issues in a navy shipyard can be complex and multifaceted. Some of the common causes include inadequate training and experience of the welders, poor equipment maintenance, and insufficient quality control measures. Other factors can include the use of incorrect welding materials, inadequate preparation of the surfaces to be welded, and poor welding technique. Additionally, the marine environment can pose unique challenges, such as high humidity, saltwater, and extreme temperatures, which can affect the welding process and the quality of the welds.Consequences of Welding Issues
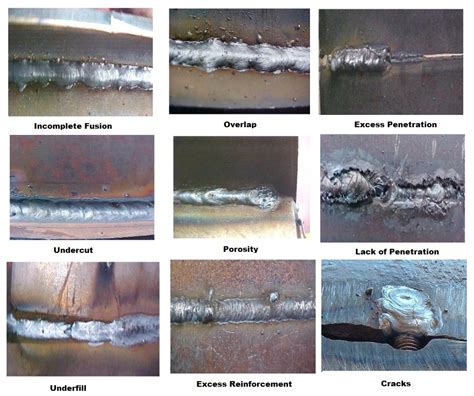
The consequences of welding issues in a navy shipyard can be severe and far-reaching. Any defects or weaknesses in the welds can compromise the safety of the ship and its crew, making it essential to identify and address any issues promptly. Additionally, welding issues can result in costly repairs, downtime, and delays, which can have significant economic and operational implications. In some cases, welding issues can even lead to the loss of the ship or its cargo, resulting in significant financial and environmental losses.
Prevention and Mitigation Strategies
To prevent and mitigate welding issues in a navy shipyard, several strategies can be employed. These include providing adequate training and experience for the welders, maintaining equipment regularly, and implementing robust quality control measures. Additionally, the use of correct welding materials, adequate preparation of the surfaces to be welded, and good welding technique can help to minimize the risk of defects and weaknesses. Regular inspection and testing of the welds can also help to identify any issues promptly, allowing for prompt repair and minimizing the risk of further damage.Best Practices for Welding in Navy Shipyard
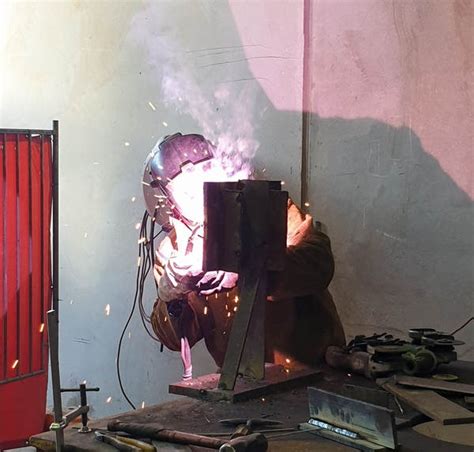
Some of the best practices for welding in a navy shipyard include following established welding procedures and guidelines, using correct welding materials, and maintaining equipment regularly. Additionally, providing adequate training and experience for the welders, implementing robust quality control measures, and conducting regular inspection and testing of the welds can help to minimize the risk of defects and weaknesses. By following these best practices, navy shipyards can help to ensure the quality and safety of the welds, reducing the risk of costly repairs, downtime, and delays.
Technological Advances in Welding
Technological advances in welding have the potential to significantly improve the quality and safety of the welds in a navy shipyard. Some of the recent advances include the use of automated welding systems, advanced welding materials, and improved inspection and testing techniques. Automated welding systems can help to improve the consistency and quality of the welds, while advanced welding materials can provide improved strength and durability. Improved inspection and testing techniques can help to identify any defects or weaknesses promptly, allowing for prompt repair and minimizing the risk of further damage.Future of Welding in Navy Shipyard
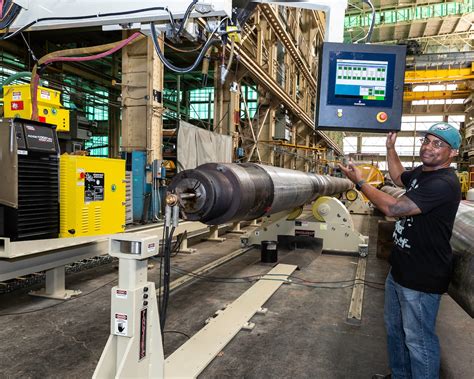
The future of welding in a navy shipyard is likely to be shaped by technological advances, changing regulatory requirements, and evolving operational needs. As the marine environment becomes increasingly complex and challenging, the need for high-quality and reliable welds will become even more critical. Navy shipyards will need to invest in the latest technologies and techniques, provide ongoing training and development for their welders, and implement robust quality control measures to ensure the quality and safety of the welds.
Conclusion and Recommendations
In conclusion, welding issues in a navy shipyard can have significant consequences, including compromising the safety of the ship and its crew, resulting in costly repairs, downtime, and delays. To prevent and mitigate these issues, it is essential to provide adequate training and experience for the welders, maintain equipment regularly, and implement robust quality control measures. By following best practices, investing in technological advances, and providing ongoing training and development, navy shipyards can help to ensure the quality and safety of the welds, reducing the risk of costly repairs, downtime, and delays.Welding in Navy Shipyard Image Gallery
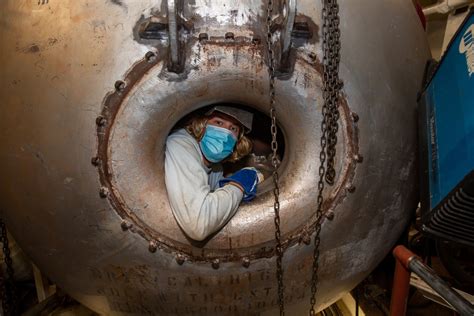

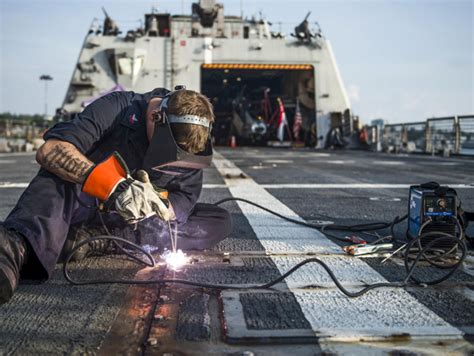
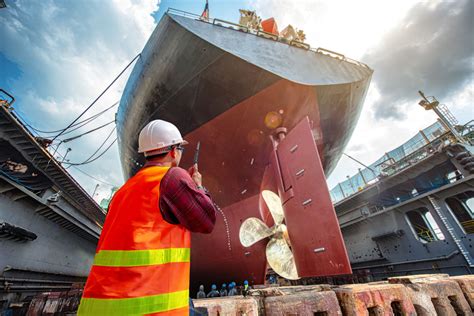
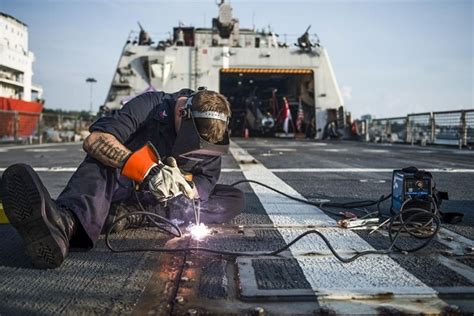
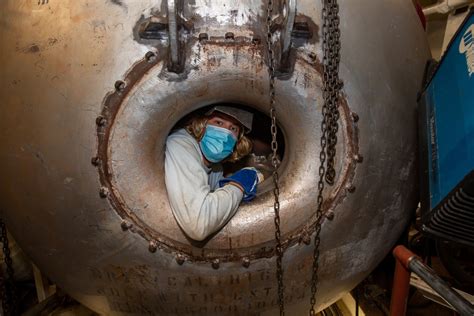
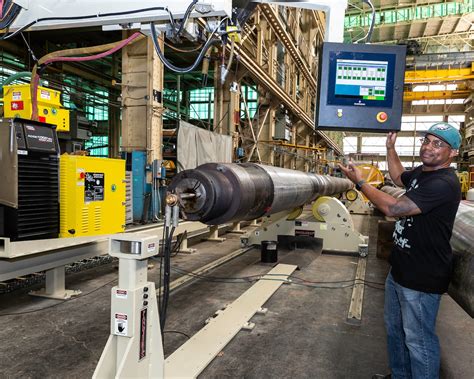
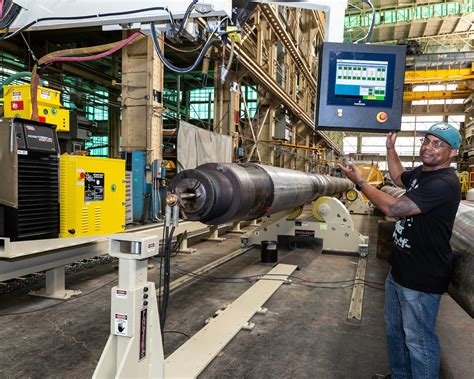
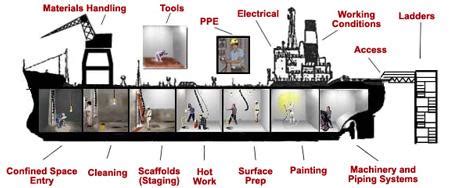
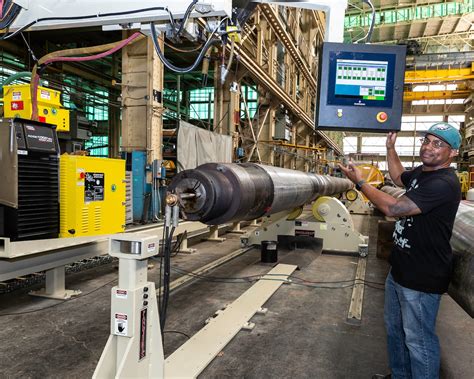
What are the common welding issues in a navy shipyard?
+The common welding issues in a navy shipyard include porosity, lack of fusion, and cracking. These issues can be caused by a variety of factors, including inadequate training, poor equipment maintenance, and insufficient quality control measures.
How can welding issues in a navy shipyard be prevented and mitigated?
+Welding issues in a navy shipyard can be prevented and mitigated by providing adequate training and experience for the welders, maintaining equipment regularly, and implementing robust quality control measures. Additionally, the use of correct welding materials, adequate preparation of the surfaces to be welded, and good welding technique can help to minimize the risk of defects and weaknesses.
What are the consequences of welding issues in a navy shipyard?
+The consequences of welding issues in a navy shipyard can be severe and far-reaching, including compromising the safety of the ship and its crew, resulting in costly repairs, downtime, and delays. In some cases, welding issues can even lead to the loss of the ship or its cargo, resulting in significant financial and environmental losses.
What are the best practices for welding in a navy shipyard?
+The best practices for welding in a navy shipyard include following established welding procedures and guidelines, using correct welding materials, and maintaining equipment regularly. Additionally, providing adequate training and experience for the welders, implementing robust quality control measures, and conducting regular inspection and testing of the welds can help to minimize the risk of defects and weaknesses.
How can technological advances improve welding in a navy shipyard?
+Technological advances in welding have the potential to significantly improve the quality and safety of the welds in a navy shipyard. Some of the recent advances include the use of automated welding systems, advanced welding materials, and improved inspection and testing techniques. These advances can help to improve the consistency and quality of the welds, reduce the risk of defects and weaknesses, and improve the overall efficiency and productivity of the welding process.
We hope this article has provided you with a comprehensive overview of the welding issues that can arise in a navy shipyard and the strategies that can be employed to prevent and mitigate them. If you have any further questions or would like to learn more about welding in a navy shipyard, please do not hesitate to contact us. Additionally, if you have any experiences or insights to share on this topic, we would be delighted to hear from you. Please feel free to comment below or share this article with others who may be interested in this topic.