Intro
Discover the 7 steps to build a Chunnel, including tunnel engineering, geotechnical analysis, and construction methods, to create a secure undersea passage with advanced tunnel boring techniques and precise project management.
The Channel Tunnel, also known as the Chunnel, is a remarkable feat of engineering that connects England and France. The idea of building a tunnel under the English Channel dates back to the 19th century, but it wasn't until the 20th century that the project became a reality. In this article, we will explore the 7 steps to build the Chunnel, a project that required meticulous planning, cutting-edge technology, and sheer determination.
The Chunnel is an impressive 50 kilometers long and took over 15,000 workers to build. The tunnel is made up of two running tunnels, one for each direction, and a smaller service tunnel in between. The project was a massive undertaking that required the collaboration of British and French engineers, contractors, and governments. The Chunnel has revolutionized travel between England and France, reducing travel time and increasing trade between the two countries.
The construction of the Chunnel was a complex process that involved several stages. From the initial planning phase to the final completion, the project took over 6 years to finish. The Chunnel is an iconic symbol of engineering excellence and a testament to human ingenuity. In this article, we will delve into the 7 steps to build the Chunnel, exploring the challenges, successes, and innovations that made this project possible.
Introduction to the Chunnel Project
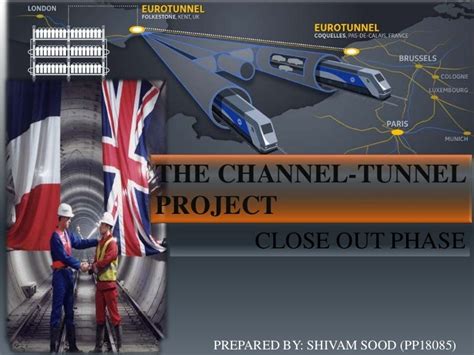
Step 1: Planning and Design
The first step in building the Chunnel was planning and design. This involved conducting feasibility studies, geological surveys, and environmental impact assessments. The engineers had to consider the geology of the English Channel, the tides, and the potential risks of building a tunnel under the sea. The planning phase took several years, during which time the engineers developed a detailed design for the tunnel and its infrastructure.Geological Challenges
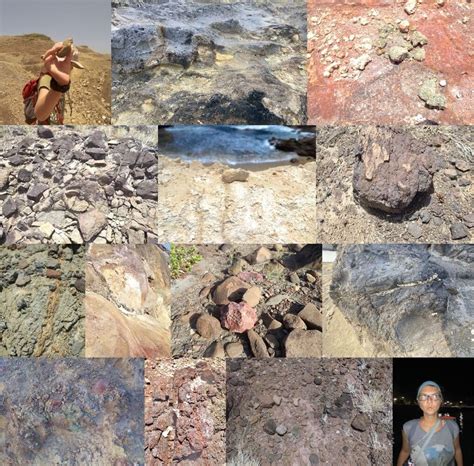
Step 2: Tunnel Boring
The second step in building the Chunnel was tunnel boring. This involved using massive tunnel boring machines (TBMs) to dig the tunnels. The TBMs were designed to cut through the rock and soil, removing the debris and creating a smooth tunnel surface. The tunnel boring process took several years, during which time the engineers encountered numerous challenges, including geological faults and equipment breakdowns.Tunnel Boring Machines
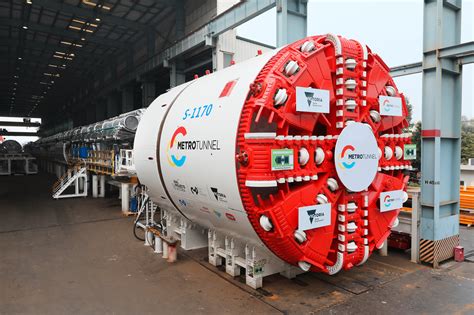
Step 3: Excavation and Removal
The third step in building the Chunnel was excavation and removal. This involved removing the rock and soil excavated by the TBMs and transporting it to the surface. The excavation process was a complex and challenging task, requiring the use of specialized equipment and techniques. The engineers had to ensure that the tunnel was stable and secure, while also removing the debris and rock in a safe and efficient manner.Excavation and Removal Process
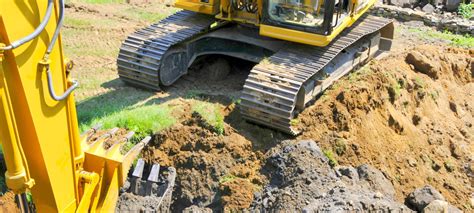
Step 4: Linings and Waterproofing
The fourth step in building the Chunnel was linings and waterproofing. This involved installing a lining system to protect the tunnel from water and other hazards. The lining system consisted of a series of interlocking concrete segments, which were designed to provide a watertight seal. The engineers also had to install a waterproofing system, which involved applying a layer of waterproof material to the tunnel surface.Linings and Waterproofing System
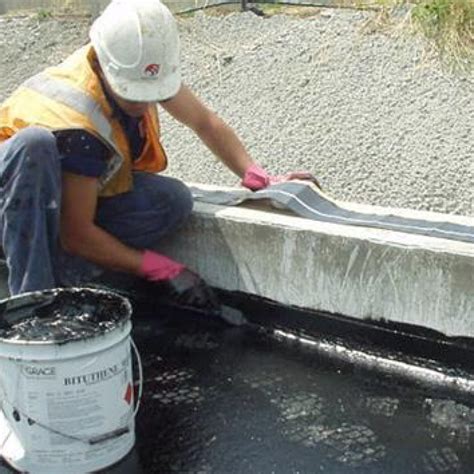
Step 5: Track and Signaling
The fifth step in building the Chunnel was track and signaling. This involved installing the rail tracks, signaling systems, and other infrastructure necessary for train operation. The engineers had to ensure that the tracks were aligned precisely, allowing for smooth and safe train travel. The signaling systems were designed to provide real-time information to train operators, ensuring safe and efficient train operation.Track and Signaling System
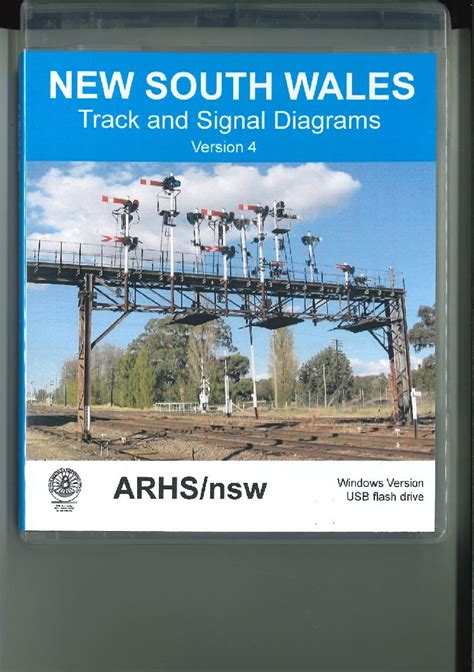
Step 6: Electrification and Ventilation
The sixth step in building the Chunnel was electrification and ventilation. This involved installing the electrical systems, ventilation systems, and other infrastructure necessary for train operation. The engineers had to ensure that the electrical systems were safe and efficient, providing power to the trains and other equipment. The ventilation systems were designed to provide a safe and healthy environment for train passengers and crew.Electrification and Ventilation System
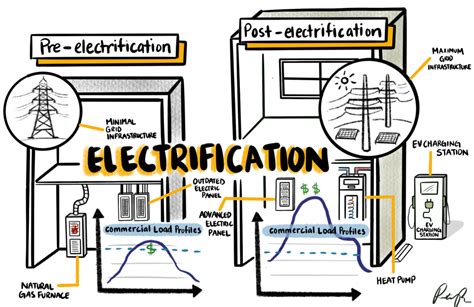
Step 7: Final Testing and Commissioning
The seventh and final step in building the Chunnel was final testing and commissioning. This involved testing the tunnel and its infrastructure, ensuring that everything was safe and functional. The engineers had to conduct a series of tests, including safety tests, performance tests, and reliability tests. The tunnel was also inspected and certified by regulatory authorities, ensuring that it met the required safety and performance standards.Final Testing and Commissioning
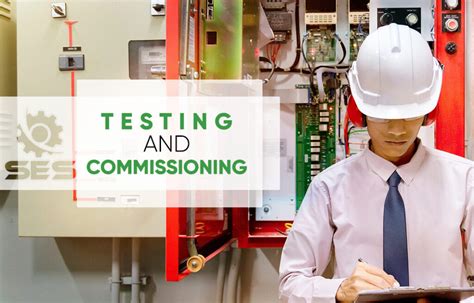
Chunnel Construction Image Gallery
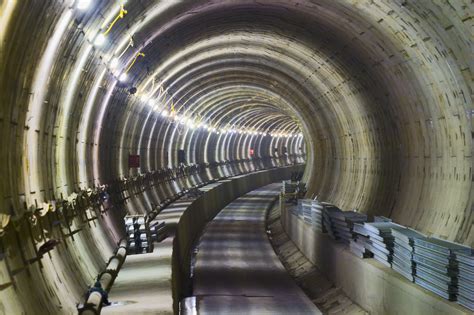
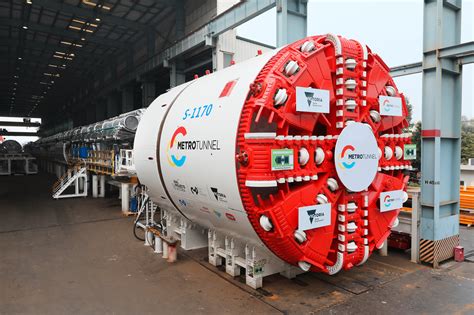
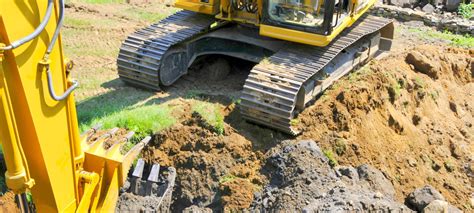
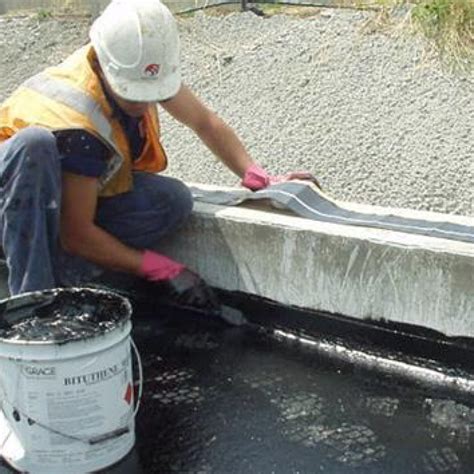
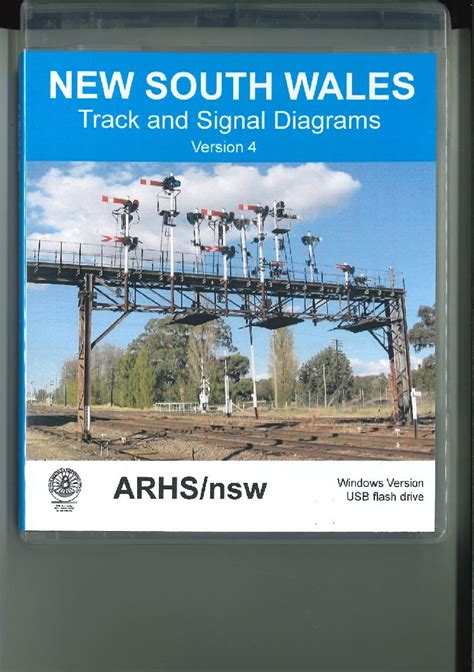
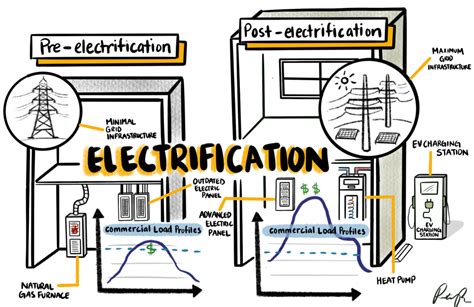
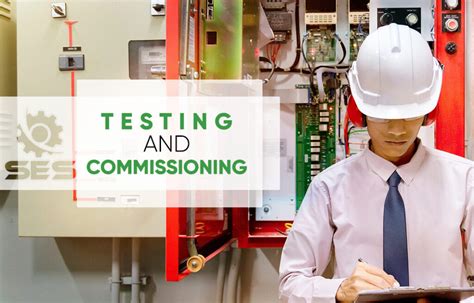
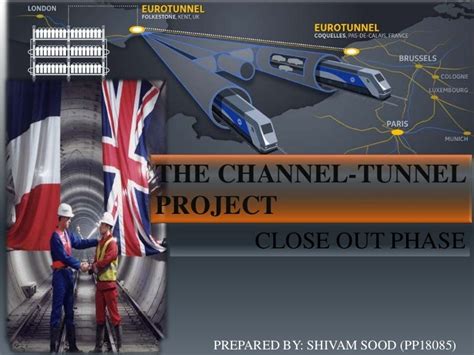
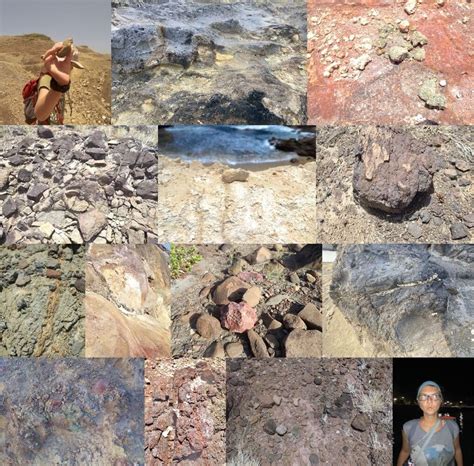
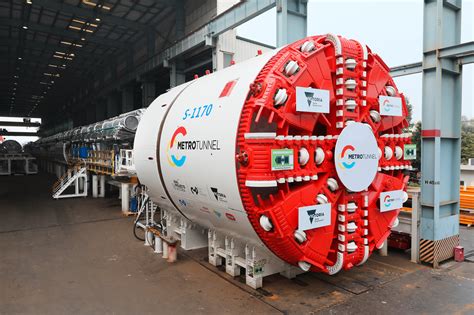
What is the length of the Chunnel?
+The Chunnel is approximately 50 kilometers long.
How long did it take to build the Chunnel?
+The Chunnel took over 6 years to build, from 1986 to 1994.
What is the purpose of the Chunnel?
+The Chunnel is a transportation tunnel that connects England and France, allowing for the passage of trains and other vehicles.
How many workers were involved in the construction of the Chunnel?
+Over 15,000 workers were involved in the construction of the Chunnel.
What are the benefits of the Chunnel?
+The Chunnel has revolutionized travel between England and France, reducing travel time and increasing trade between the two countries.
In conclusion, the construction of the Chunnel was a complex and challenging project that required meticulous planning, cutting-edge technology, and sheer determination. The 7 steps to build the Chunnel, from planning and design to final testing and commissioning, were critical components of the project. The Chunnel is an iconic symbol of engineering excellence and a testament to human ingenuity. We hope that this article has provided you with a comprehensive understanding of the Chunnel project and its significance. If you have any further questions or would like to learn more about the Chunnel, please do not hesitate to contact us. We would be happy to hear from you and provide you with any additional information you may need.