Intro
Discover the risks of faulty welds in Navy warships, including structural failures, corrosion, and naval vessel integrity compromises, affecting shipbuilding and maritime safety standards.
The importance of ensuring the structural integrity of naval warships cannot be overstated. These vessels are designed to withstand the harsh conditions of the open sea, protect their crew, and perform a variety of critical missions. However, recent concerns have been raised regarding the presence of faulty welds in some Navy warships. This issue has significant implications for the safety and effectiveness of these vessels, and it is essential to understand the causes, consequences, and potential solutions to this problem. As we delve into the world of naval engineering and the complexities of shipbuilding, it becomes clear that the issue of faulty welds is a multifaceted one that requires careful consideration and attention.
The construction of a naval warship involves a multitude of complex processes, including design, materials selection, and fabrication. Welding is a critical component of this process, as it is used to join the various components of the ship's hull and superstructure. However, welding is a highly skilled craft that requires great attention to detail and a thorough understanding of the materials being used. When welds are not properly executed, they can create weaknesses in the ship's structure, which can have serious consequences in the event of an emergency or combat situation. The potential risks associated with faulty welds include reduced structural integrity, increased risk of damage or flooding, and compromised crew safety.
As the Navy continues to face evolving threats and operational demands, the need for reliable and effective warships has never been more pressing. The presence of faulty welds in some of these vessels is a cause for concern, as it can impact their ability to perform their intended missions and protect their crew. Furthermore, the financial and resource implications of repairing or replacing faulty welds can be significant, making it essential to address this issue proactively. By examining the causes and consequences of faulty welds, as well as potential solutions and mitigation strategies, we can work towards ensuring the safety and effectiveness of our naval warships.
Causes of Faulty Welds in Navy Warships
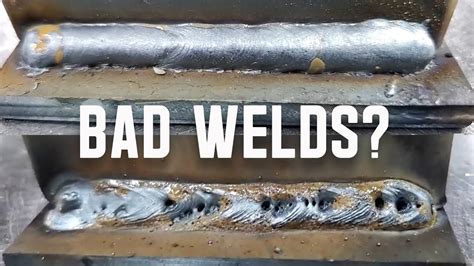
Some of the key factors that can contribute to faulty welds include:
- Inadequate welder training or experience
- Insufficient quality control measures
- Use of substandard materials
- Complex warship designs
- Rapid production and deployment schedules
- Inadequate inspection and testing procedures By addressing these factors and implementing effective mitigation strategies, the Navy can reduce the risk of faulty welds and ensure the structural integrity of its warships.
Consequences of Faulty Welds in Navy Warships
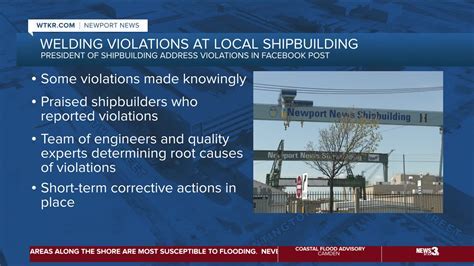
Some of the key consequences of faulty welds include:
- Reduced structural integrity
- Increased risk of damage or flooding
- Compromised crew safety
- Reduced mission effectiveness
- Increased maintenance and repair costs
- Potential for catastrophic failure By understanding the potential consequences of faulty welds, the Navy can take steps to mitigate these risks and ensure the safety and effectiveness of its warships.
Solutions and Mitigation Strategies
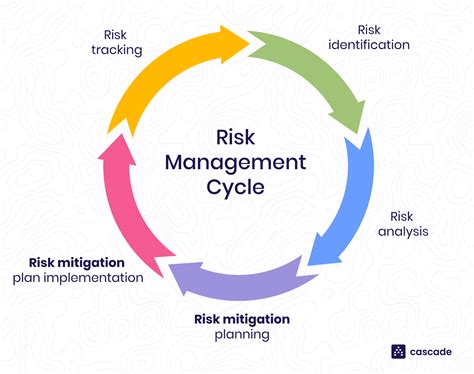
Some of the key solutions and mitigation strategies include:
- Enhanced welder training and certification programs
- Improved quality control measures
- Advanced inspection and testing technologies
- Robust and resilient warship designs
- Effective maintenance and repair procedures
- Regular inspections and assessments
- Implementation of industry best practices By implementing these solutions and mitigation strategies, the Navy can reduce the risk of faulty welds and ensure the structural integrity of its warships.
Best Practices for Welding in Navy Warships
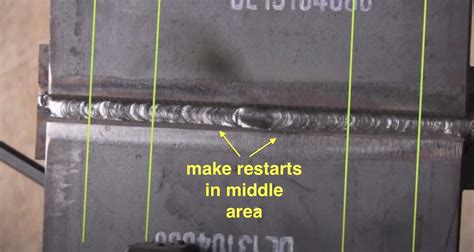
Some of the key best practices for welding include:
- Use of qualified and certified welders
- Adherence to established welding procedures
- Robust quality control measures
- Advanced welding technologies and techniques
- Real-time monitoring and inspection tools
- Regular training and certification programs
- Implementation of industry best practices By following these best practices, the Navy can ensure the quality and integrity of welds in its warships and reduce the risk of faulty welds.
Future Directions for Welding in Navy Warships
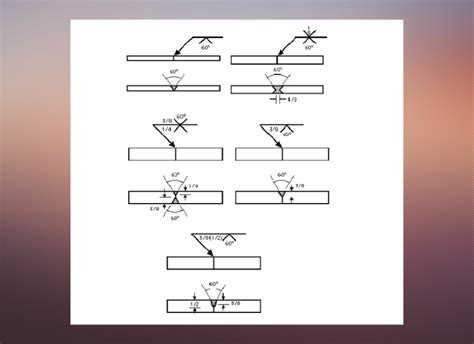
Some of the key future directions for welding include:
- Use of advanced materials and technologies
- Additive manufacturing and nanomaterials
- More efficient and effective welding processes
- Integrated and holistic approaches to shipbuilding
- Advanced inspection and testing technologies
- Real-time monitoring and inspection tools
- Implementation of industry best practices By exploring these future directions, the Navy can stay at the forefront of welding technology and ensure the continued safety and effectiveness of its warships.
Gallery of Navy Warship Welding
Navy Warship Welding Image Gallery
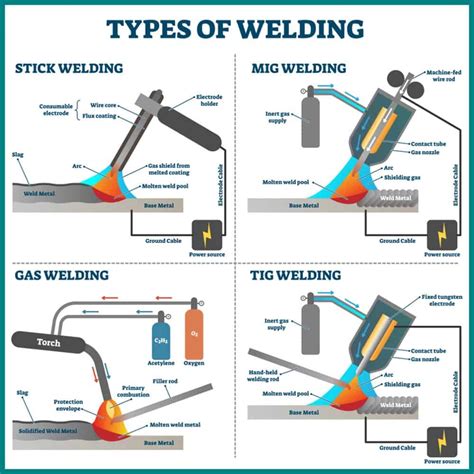
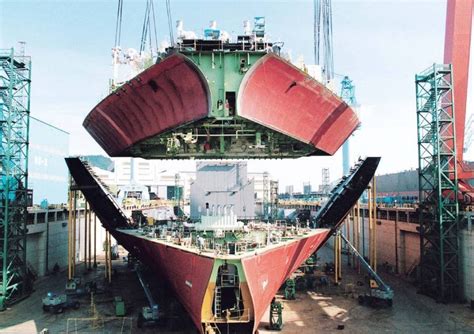
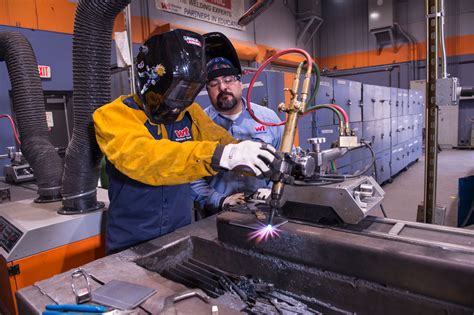
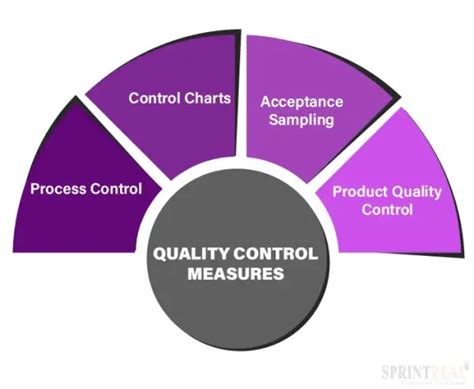
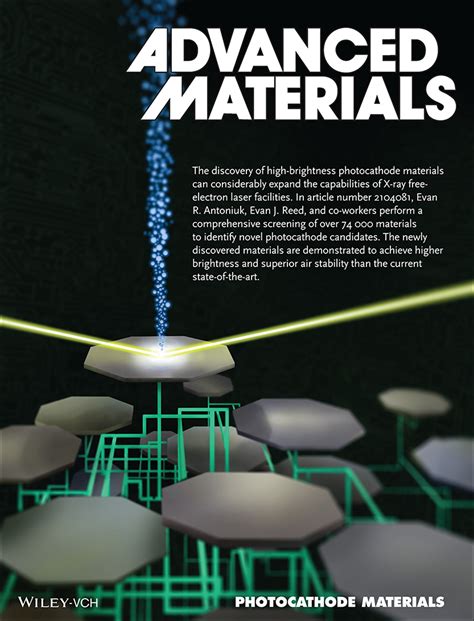
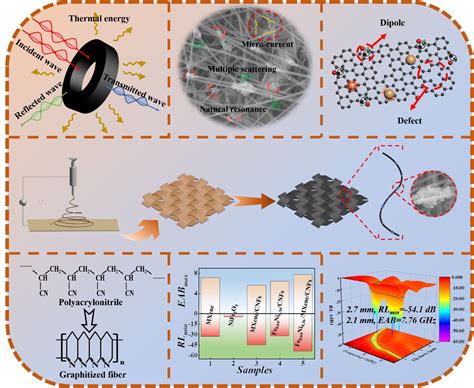
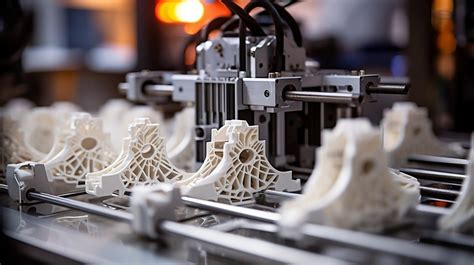
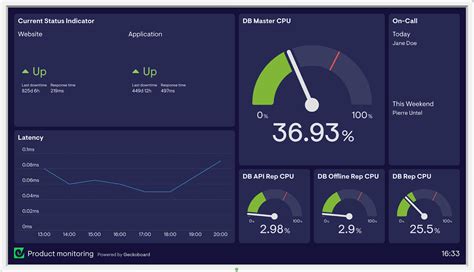
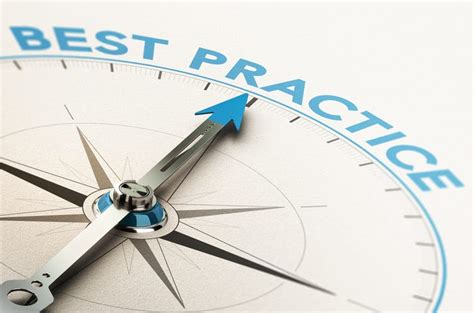
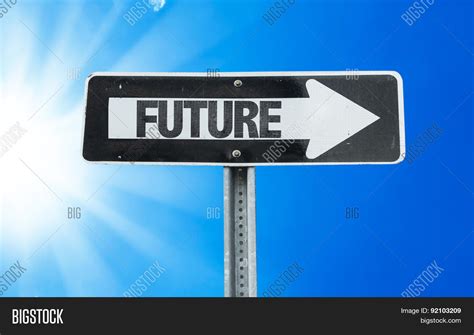
What are the causes of faulty welds in Navy warships?
+The causes of faulty welds in Navy warships are varied and complex, including inadequate training or experience among welders, insufficient quality control measures, and the use of substandard materials.
What are the consequences of faulty welds in Navy warships?
+The consequences of faulty welds in Navy warships can be severe and far-reaching, including reduced structural integrity, increased risk of damage or flooding, and compromised crew safety.
What are the best practices for welding in Navy warships?
+The best practices for welding in Navy warships include the use of qualified and certified welders, adherence to established welding procedures, and the implementation of robust quality control measures.
What are the future directions for welding in Navy warships?
+The future directions for welding in Navy warships include the use of advanced materials and technologies, such as additive manufacturing and nanomaterials, as well as the implementation of more efficient and effective welding processes.
How can the Navy ensure the quality and integrity of welds in its warships?
+The Navy can ensure the quality and integrity of welds in its warships by implementing effective quality control measures, providing regular training and certification programs for welders, and adopting advanced welding technologies and techniques.
In conclusion, the issue of faulty welds in Navy warships is a complex and multifaceted one that requires careful consideration and attention. By understanding the causes, consequences, and potential solutions to this problem, the Navy can take steps to mitigate these risks and ensure the safety and effectiveness of its warships. As we move forward, it is essential to continue exploring new technologies and techniques, adopting industry best practices, and implementing effective quality control measures to ensure the quality and integrity of welds in Navy warships. We invite you to share your thoughts and comments on this critical issue, and to join us in our efforts to ensure the continued safety and effectiveness of our naval warships.