Intro
Master heavy equipment operation with 5 drills job techniques, including excavation, construction, and earthmoving methods, to boost efficiency and safety on the job site.
The world of heavy equipment is a fascinating one, with a wide range of machines designed to tackle various tasks. Among these, drills are some of the most crucial, playing a key role in construction, mining, and other industries. In this article, we'll delve into the world of drills used in heavy equipment operations, exploring their types, applications, and importance.
Heavy equipment drills are designed to handle tough tasks, such as breaking through hard rock, drilling deep holes, and extracting valuable resources. These machines are often massive, with some weighing tens of thousands of pounds and standing multiple stories tall. Despite their size, they are incredibly precise, allowing operators to drill into the earth with accuracy and control. The importance of drills in heavy equipment operations cannot be overstated, as they enable the extraction of resources, the construction of infrastructure, and the development of new projects.
The use of drills in heavy equipment operations has a long history, dating back to the early days of mining and construction. Over time, these machines have evolved to become more powerful, efficient, and precise, with advancements in technology and design leading to improved performance and productivity. Today, drills are used in a wide range of applications, from oil and gas extraction to construction and mining. They are also used in environmental remediation, such as cleaning up contaminated soil and groundwater.
Types of Drills Used in Heavy Equipment Operations
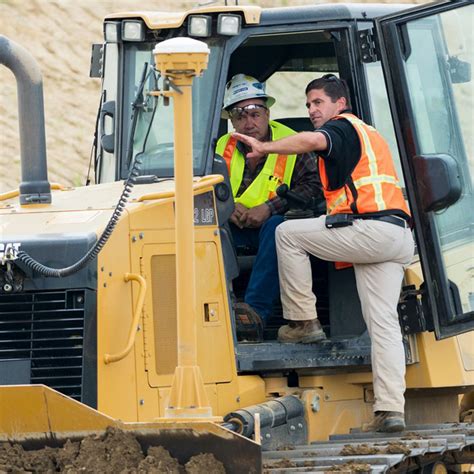
There are several types of drills used in heavy equipment operations, each designed for specific tasks and applications. Some of the most common types include:
- Rotary drills: These drills use a rotating bit to break through rock and soil, and are commonly used in oil and gas extraction, as well as construction and mining.
- Percussion drills: These drills use a hammering action to break through rock and soil, and are often used in mining and construction applications.
- Diamond drills: These drills use a diamond-coated bit to drill through hard rock and are commonly used in mining and construction applications.
- Top-hammer drills: These drills use a hammering action to break through rock and soil, and are often used in mining and construction applications.
- Down-the-hole drills: These drills use a hammering action to break through rock and soil, and are commonly used in mining and construction applications.
Applications of Drills in Heavy Equipment Operations
The applications of drills in heavy equipment operations are diverse and widespread. Some of the most common applications include: * Oil and gas extraction: Drills are used to extract oil and gas from the earth, with rotary drills being the most common type used in this application. * Construction: Drills are used in construction to drill holes for foundation work, such as piers and caissons, as well as to drill through rock and soil for tunnels and other underground structures. * Mining: Drills are used in mining to extract minerals and other resources from the earth, with percussion and rotary drills being the most common types used in this application. * Environmental remediation: Drills are used in environmental remediation to clean up contaminated soil and groundwater, with diamond and rotary drills being the most common types used in this application.Benefits of Using Drills in Heavy Equipment Operations
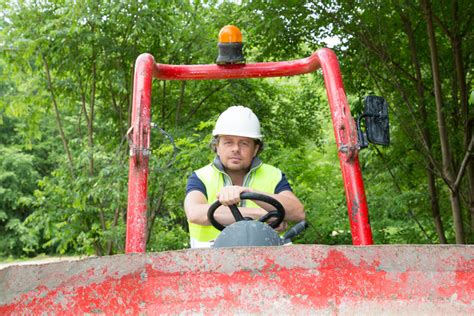
The benefits of using drills in heavy equipment operations are numerous and significant. Some of the most important benefits include:
- Increased productivity: Drills enable operators to drill into the earth quickly and efficiently, increasing productivity and reducing downtime.
- Improved accuracy: Drills allow operators to drill into the earth with precision and control, reducing the risk of errors and improving overall accuracy.
- Reduced costs: Drills can help reduce costs by minimizing the amount of material that needs to be removed, as well as by reducing the amount of time and labor required to complete a project.
- Enhanced safety: Drills can help improve safety by reducing the risk of accidents and injuries, as well as by minimizing the amount of manual labor required to complete a project.
Steps to Operate a Drill in Heavy Equipment Operations
Operating a drill in heavy equipment operations requires careful planning and execution. Some of the key steps to operate a drill include: * Pre-operational checks: Before operating a drill, it's essential to perform pre-operational checks to ensure that the machine is in good working condition. * Site preparation: The site must be prepared before drilling can begin, including clearing the area of debris and obstacles. * Drilling: The drill is then used to drill into the earth, with the operator carefully controlling the machine to ensure accuracy and precision. * Post-operational checks: After drilling is complete, post-operational checks must be performed to ensure that the machine is in good working condition and that the site is safe and secure.Common Challenges Faced by Drill Operators
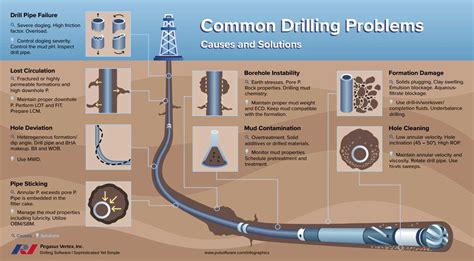
Drill operators face a range of challenges when operating drills in heavy equipment operations. Some of the most common challenges include:
- Difficult terrain: Drilling in difficult terrain, such as rocky or hilly areas, can be challenging and require specialized equipment and techniques.
- Hard rock: Drilling through hard rock can be challenging and require specialized equipment and techniques.
- Limited access: Drilling in areas with limited access, such as urban areas or areas with restricted access, can be challenging and require specialized equipment and techniques.
- Environmental concerns: Drilling can have environmental impacts, such as noise pollution and habitat disruption, and operators must take steps to minimize these impacts.
Best Practices for Drill Maintenance
Regular maintenance is essential to ensure that drills are operating efficiently and effectively. Some best practices for drill maintenance include: * Regular lubrication: Drills require regular lubrication to ensure that moving parts are well-lubricated and to prevent wear and tear. * Filter maintenance: Air and fuel filters must be regularly cleaned and replaced to ensure that the drill is operating efficiently and effectively. * Battery maintenance: Batteries must be regularly checked and maintained to ensure that they are holding a charge and operating efficiently. * Operator training: Operators must be properly trained to operate and maintain drills, including regular training on safety procedures and best practices.Future of Drills in Heavy Equipment Operations
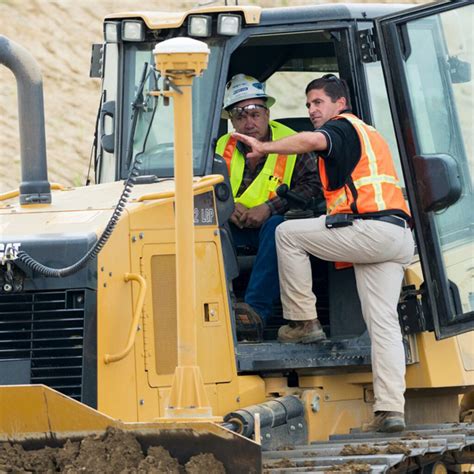
The future of drills in heavy equipment operations is exciting and rapidly evolving. Some of the key trends and developments that are shaping the future of drills include:
- Automation: Automation is becoming increasingly common in drilling operations, with automated systems able to drill more efficiently and accurately than human operators.
- Electrification: Electrification is becoming increasingly common in drilling operations, with electric drills offering improved efficiency and reduced environmental impacts.
- Digitalization: Digitalization is becoming increasingly common in drilling operations, with digital systems able to monitor and control drilling operations in real-time.
- Sustainability: Sustainability is becoming increasingly important in drilling operations, with operators seeking to minimize environmental impacts and reduce waste.
Gallery of Drills Used in Heavy Equipment Operations
Drills Used in Heavy Equipment Operations Image Gallery
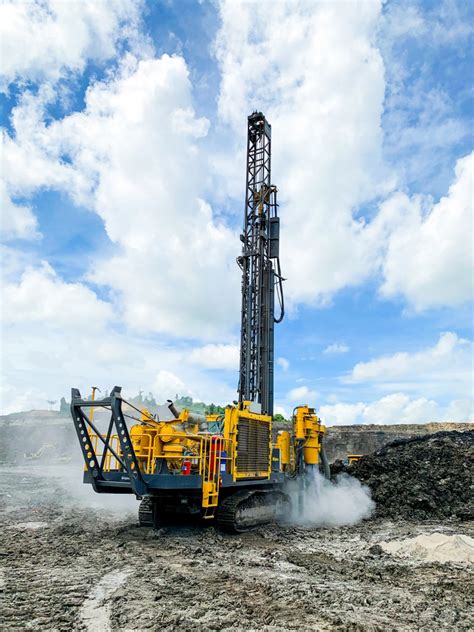
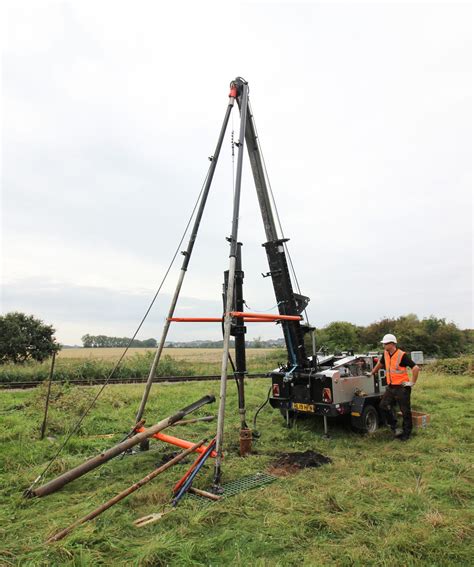
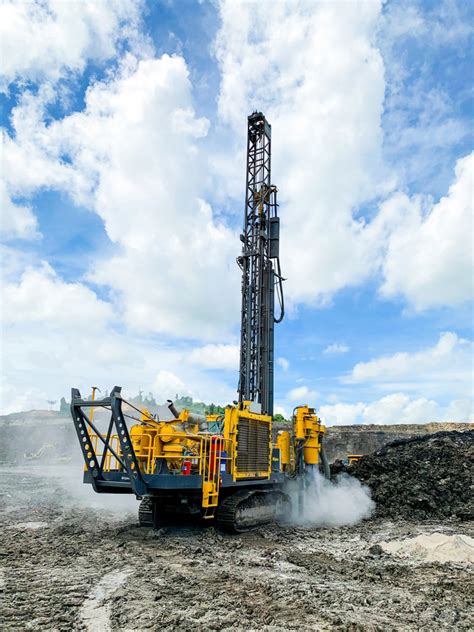
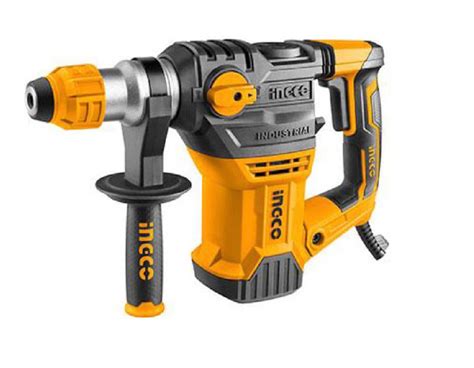
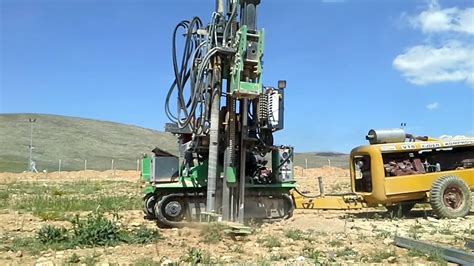
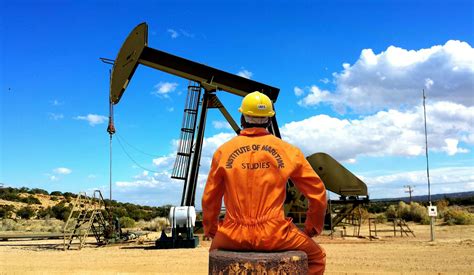
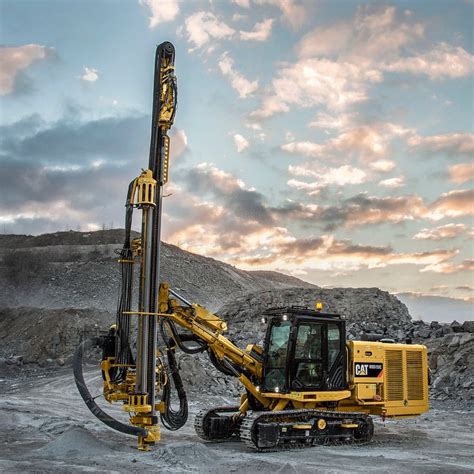
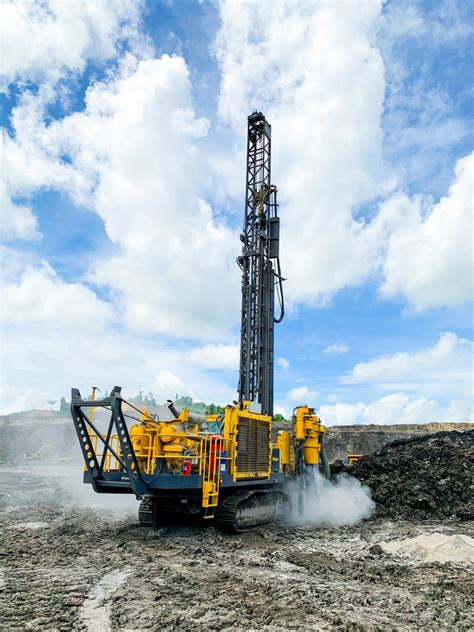
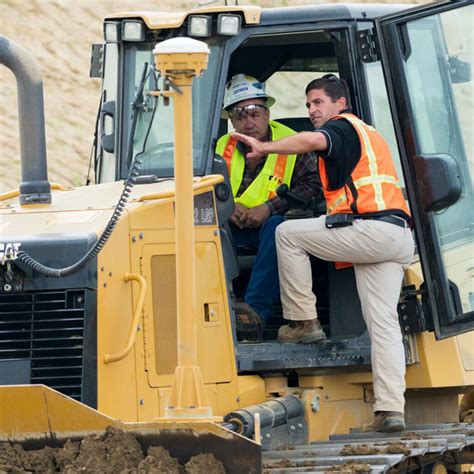
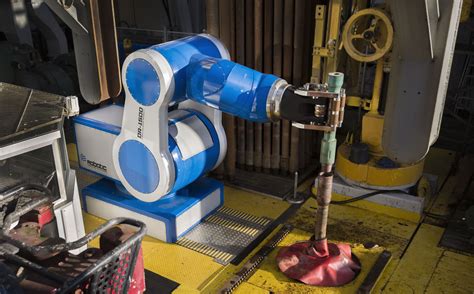
Frequently Asked Questions
What are the different types of drills used in heavy equipment operations?
+The different types of drills used in heavy equipment operations include rotary drills, percussion drills, diamond drills, top-hammer drills, and down-the-hole drills.
What are the applications of drills in heavy equipment operations?
+The applications of drills in heavy equipment operations include oil and gas extraction, construction, mining, and environmental remediation.
What are the benefits of using drills in heavy equipment operations?
+The benefits of using drills in heavy equipment operations include increased productivity, improved accuracy, reduced costs, and enhanced safety.
What are the common challenges faced by drill operators?
+The common challenges faced by drill operators include difficult terrain, hard rock, limited access, and environmental concerns.
What is the future of drills in heavy equipment operations?
+The future of drills in heavy equipment operations is exciting and rapidly evolving, with trends and developments including automation, electrification, digitalization, and sustainability.
In conclusion, drills play a vital role in heavy equipment operations, enabling operators to drill into the earth with precision and control. With a range of types and applications, drills are used in various industries, including oil and gas extraction, construction, mining, and environmental remediation. As technology continues to evolve, the future of drills in heavy equipment operations is likely to be shaped by trends such as automation, electrification, digitalization, and sustainability. We hope this article has provided you with a comprehensive overview of drills used in heavy equipment operations. If you have any further questions or would like to share your experiences with drills, please don't hesitate to comment below. Additionally, if you found this article informative, please share it with your friends and colleagues who may be interested in learning more about drills used in heavy equipment operations.