Intro
Learn Mig welding stainless steel techniques, including metal preparation, shielding gases, and weld finishing, to achieve strong, corrosion-resistant joints in various stainless steel alloys and applications.
Mig welding stainless steel is a complex process that requires attention to detail, the right equipment, and a thorough understanding of the materials being used. Stainless steel is a popular choice for many industries, including construction, automotive, and food processing, due to its corrosion resistance, durability, and aesthetic appeal. However, welding stainless steel can be challenging, especially when using the Mig welding process. In this article, we will explore the importance of Mig welding stainless steel, the benefits and challenges associated with this process, and provide tips and guidelines for achieving high-quality welds.
The importance of Mig welding stainless steel cannot be overstated. Stainless steel is used in a wide range of applications, from kitchen utensils and medical equipment to automotive and aerospace components. The ability to weld stainless steel effectively is crucial for many industries, as it allows for the creation of complex shapes and structures that are both strong and corrosion-resistant. Mig welding is a popular choice for welding stainless steel due to its speed, efficiency, and versatility. However, it requires specialized equipment and techniques to produce high-quality welds.
Mig welding stainless steel requires a thorough understanding of the materials being used, including the type of stainless steel, the thickness of the material, and the desired weld properties. There are several types of stainless steel, including austenitic, ferritic, and martensitic, each with its own unique characteristics and welding requirements. Austenitic stainless steel, for example, is the most common type of stainless steel and is known for its corrosion resistance and weldability. However, it can be prone to distortion and warping during the welding process, which requires careful control of heat input and welding technique.
Mig Welding Process
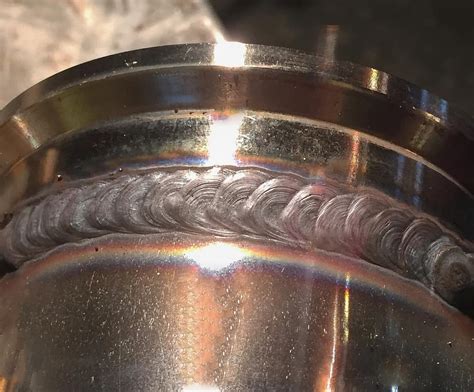
The Mig welding process involves the use of a continuous wire feed, a welding gun, and a shielding gas to protect the arc and molten metal from atmospheric gases. The wire feed is typically made of a stainless steel alloy that matches the composition of the base metal, and the shielding gas is usually a mixture of argon and carbon dioxide. The welding gun is designed to provide a consistent and controlled heat input, which is critical for producing high-quality welds.
Benefits of Mig Welding Stainless Steel
The benefits of Mig welding stainless steel include its speed, efficiency, and versatility. Mig welding is a high-speed process that can produce long, continuous welds with minimal distortion and warping. It is also a highly efficient process, as it uses a continuous wire feed and a shielding gas to minimize waste and reduce the risk of porosity and other defects. Additionally, Mig welding can be used to weld a wide range of stainless steel alloys and thicknesses, making it a versatile process for many industries.Challenges of Mig Welding Stainless Steel
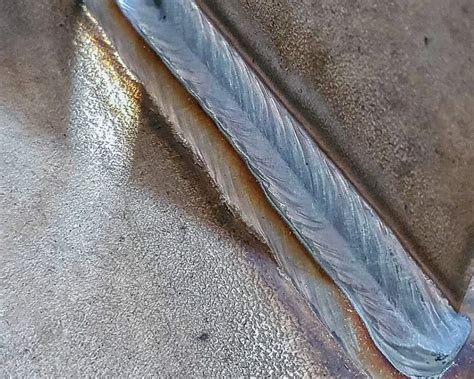
Despite its many benefits, Mig welding stainless steel can be challenging. One of the main challenges is the risk of distortion and warping, which can occur due to the high heat input and thermal expansion of the metal. This can be mitigated by using a low-heat input welding technique, such as pulse welding, and by controlling the welding speed and wire feed rate. Another challenge is the risk of porosity and other defects, which can occur due to the presence of atmospheric gases and moisture in the welding area. This can be mitigated by using a high-quality shielding gas and by maintaining a clean and dry welding environment.
Tips and Guidelines for Mig Welding Stainless Steel
To achieve high-quality welds when Mig welding stainless steel, it is essential to follow some tips and guidelines. These include:- Using a high-quality welding gun and wire feed system
- Selecting the right shielding gas and maintaining a consistent gas flow
- Controlling the welding speed and wire feed rate to minimize distortion and warping
- Maintaining a clean and dry welding environment to prevent porosity and other defects
- Using a low-heat input welding technique, such as pulse welding, to minimize thermal expansion and distortion
Equipment and Materials Needed
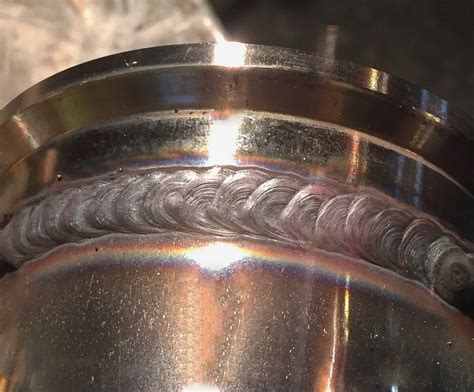
To Mig weld stainless steel, you will need a range of equipment and materials, including:
- A Mig welding machine and welding gun
- A wire feed system and stainless steel wire
- A shielding gas and gas regulator
- A welding helmet and safety glasses
- A welding table and clamping system
- Stainless steel alloys and thicknesses to be welded
Step-by-Step Guide to Mig Welding Stainless Steel
To Mig weld stainless steel, follow these steps:- Prepare the welding area by cleaning and degreasing the metal surfaces.
- Set up the welding equipment, including the Mig welding machine, welding gun, and wire feed system.
- Select the right shielding gas and maintain a consistent gas flow.
- Control the welding speed and wire feed rate to minimize distortion and warping.
- Maintain a clean and dry welding environment to prevent porosity and other defects.
- Use a low-heat input welding technique, such as pulse welding, to minimize thermal expansion and distortion.
- Monitor the weld pool and adjust the welding technique as needed to achieve a high-quality weld.
Common Mistakes to Avoid
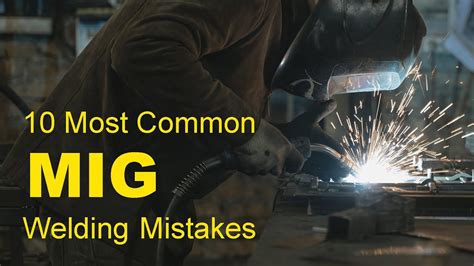
When Mig welding stainless steel, there are several common mistakes to avoid, including:
- Using the wrong shielding gas or maintaining an inconsistent gas flow
- Failing to control the welding speed and wire feed rate, resulting in distortion and warping
- Not maintaining a clean and dry welding environment, resulting in porosity and other defects
- Using a high-heat input welding technique, resulting in thermal expansion and distortion
- Not monitoring the weld pool and adjusting the welding technique as needed
Best Practices for Mig Welding Stainless Steel
To achieve high-quality welds when Mig welding stainless steel, it is essential to follow best practices, including:- Using a high-quality welding gun and wire feed system
- Selecting the right shielding gas and maintaining a consistent gas flow
- Controlling the welding speed and wire feed rate to minimize distortion and warping
- Maintaining a clean and dry welding environment to prevent porosity and other defects
- Using a low-heat input welding technique, such as pulse welding, to minimize thermal expansion and distortion
Gallery of Mig Welding Stainless Steel
Mig Welding Stainless Steel Image Gallery
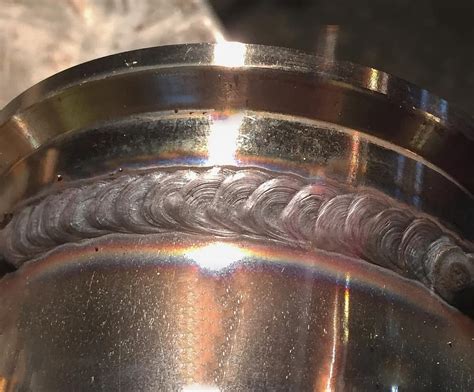
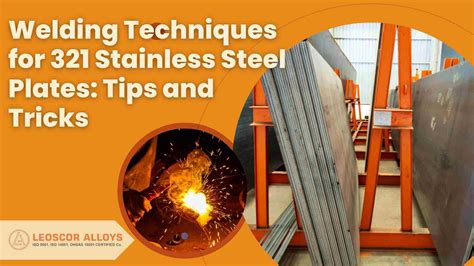
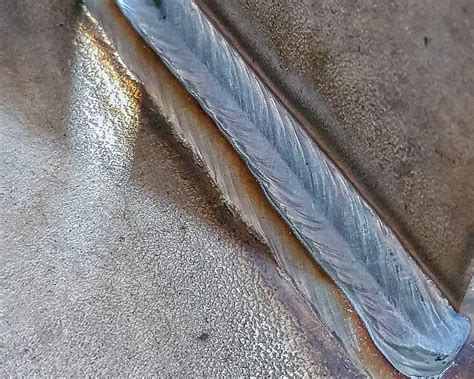
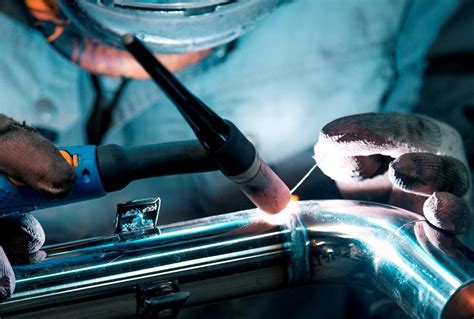
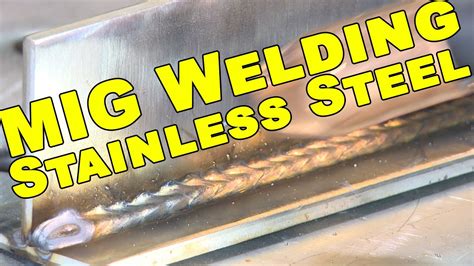
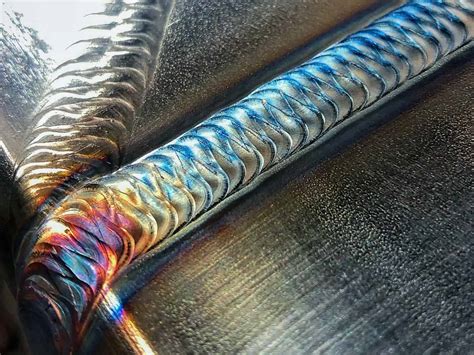
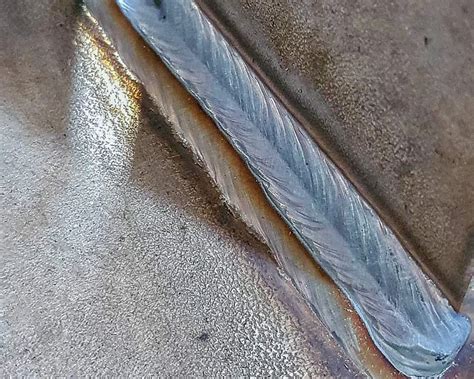
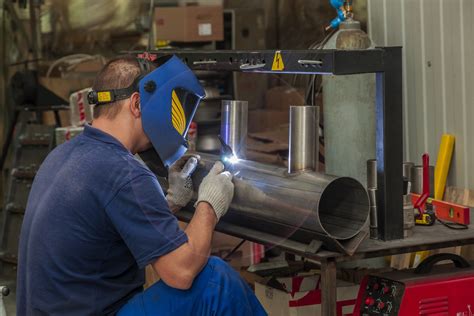
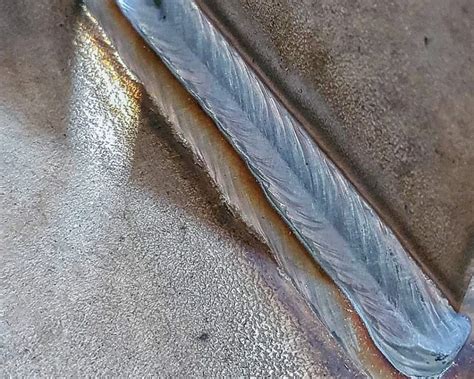
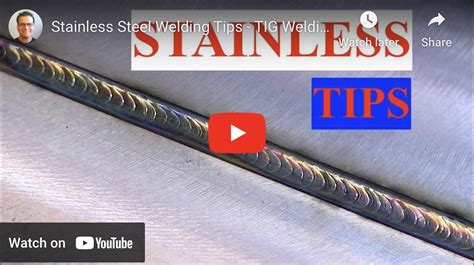
Frequently Asked Questions
What is the best shielding gas for Mig welding stainless steel?
+The best shielding gas for Mig welding stainless steel is a mixture of argon and carbon dioxide.
What is the most common type of stainless steel used in Mig welding?
+The most common type of stainless steel used in Mig welding is austenitic stainless steel.
What are the benefits of using a low-heat input welding technique when Mig welding stainless steel?
+The benefits of using a low-heat input welding technique when Mig welding stainless steel include minimizing thermal expansion and distortion, and reducing the risk of porosity and other defects.
What are the common mistakes to avoid when Mig welding stainless steel?
+The common mistakes to avoid when Mig welding stainless steel include using the wrong shielding gas, failing to control the welding speed and wire feed rate, and not maintaining a clean and dry welding environment.
What are the best practices for Mig welding stainless steel?
+The best practices for Mig welding stainless steel include using a high-quality welding gun and wire feed system, selecting the right shielding gas, controlling the welding speed and wire feed rate, and maintaining a clean and dry welding environment.
In conclusion, Mig welding stainless steel is a complex process that requires attention to detail, the right equipment, and a thorough understanding of the materials being used. By following the tips and guidelines outlined in this article, and by avoiding common mistakes, you can achieve high-quality welds that meet the requirements of your project. Whether you are a seasoned welder or just starting out, it is essential to stay up-to-date with the latest techniques and best practices for Mig welding stainless steel. Share your thoughts and experiences with Mig welding stainless steel in the comments below, and don't forget to share this article with your friends and colleagues who may be interested in learning more about this topic.