Intro
Unlock expert 3D print Lockheed engine tips, including design optimization, material selection, and printing techniques for aerospace models, using additive manufacturing and advanced CAD software.
The world of 3D printing has revolutionized the way we approach manufacturing and engineering, allowing for the creation of complex and customized parts with unprecedented ease. One of the most exciting applications of 3D printing is in the aerospace industry, where companies like Lockheed Martin are leveraging this technology to produce innovative and highly efficient engine components. In this article, we will delve into the world of 3D printing Lockheed engine tips, exploring the benefits, challenges, and future directions of this cutting-edge technology.
The importance of 3D printing in the aerospace industry cannot be overstated. Traditional manufacturing methods often involve significant lead times, high costs, and limited design flexibility, which can hinder the development of new engine technologies. 3D printing, on the other hand, enables the rapid production of complex geometries and customized parts, reducing production time and costs while improving overall performance. Lockheed Martin, a leading player in the aerospace industry, has been at the forefront of 3D printing innovation, leveraging this technology to produce a range of engine components, including engine tips.
Introduction to 3D Printing Lockheed Engine Tips
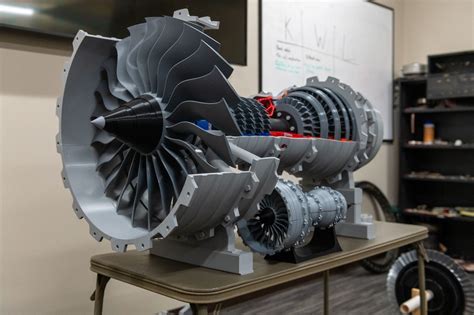
Benefits of 3D Printing Lockheed Engine Tips
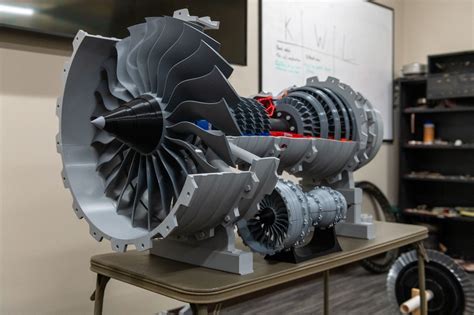
Improved Performance
3D printing Lockheed engine tips enables the creation of complex geometries that can improve engine performance. For example, the use of lattice structures and optimized aerodynamic shapes can reduce drag and increase thrust, resulting in improved fuel efficiency and reduced emissions. Additionally, 3D printing allows for the integration of advanced materials and cooling systems, which can improve engine durability and reduce maintenance costs.Reduced Weight
3D printing Lockheed engine tips also enables the creation of lightweight engine components, which can significantly reduce the overall weight of the engine. This is achieved through the use of advanced materials and optimized design geometries, which can minimize material usage while maintaining structural integrity. Reduced weight can result in improved fuel efficiency, reduced emissions, and increased payload capacity.Challenges and Limitations
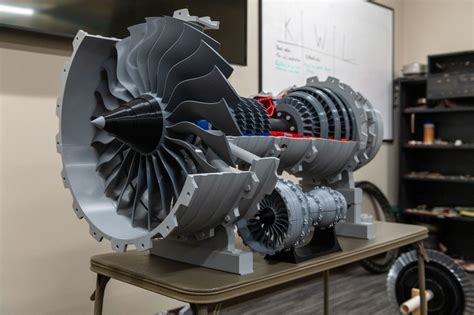
Material Limitations
Another challenge associated with 3D printing Lockheed engine tips is the limited availability of suitable materials. While a range of materials can be used for 3D printing, including metals, polymers, and ceramics, the properties of these materials can vary significantly. For example, some materials may not have the required strength, durability, or thermal resistance for engine operation, which can limit their use in certain applications.Regulatory Framework
The regulatory framework surrounding 3D printing is also evolving, with ongoing efforts to develop standards and guidelines for the use of this technology in the aerospace industry. Lockheed Martin and other companies must navigate this regulatory landscape, ensuring that their 3D printing operations meet the required safety and quality standards.Future Directions
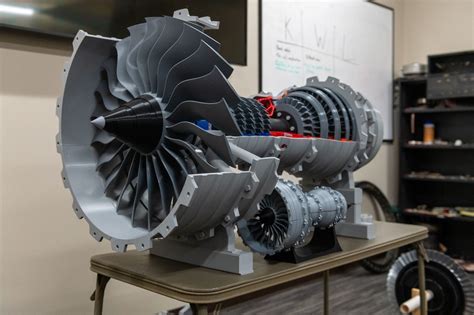
Advanced Materials
The development of advanced materials is critical to the future of 3D printing Lockheed engine tips. Researchers are exploring the use of new materials, such as advanced composites and smart materials, which can offer improved strength, durability, and thermal resistance. These materials can enable the creation of more complex geometries and customized shapes, resulting in improved engine performance and efficiency.Digital Twinning
Digital twinning is another area of focus, which involves the creation of virtual models of engine components and systems. These models can be used to simulate engine operation, optimize performance, and predict maintenance requirements. Digital twinning can also enable the creation of customized engine components, tailored to specific operational requirements and environmental conditions.3D Printing Lockheed Engine Tips Image Gallery

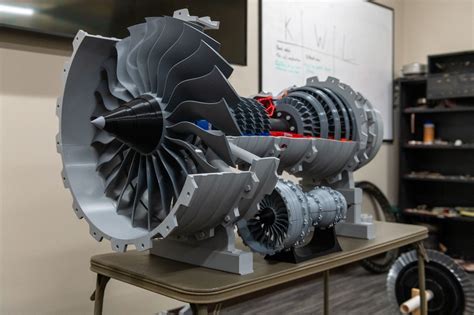
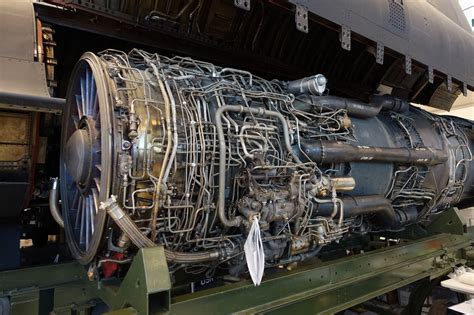
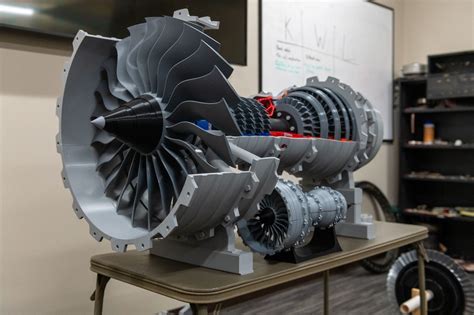
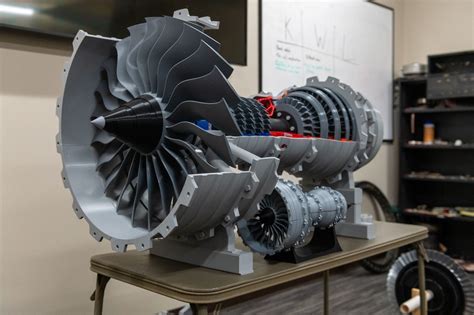
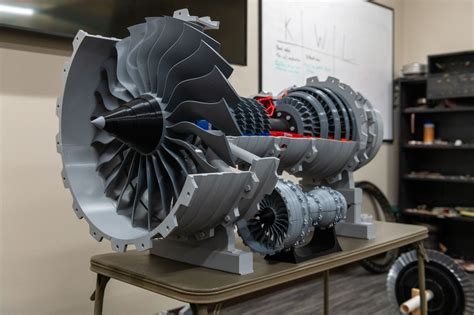
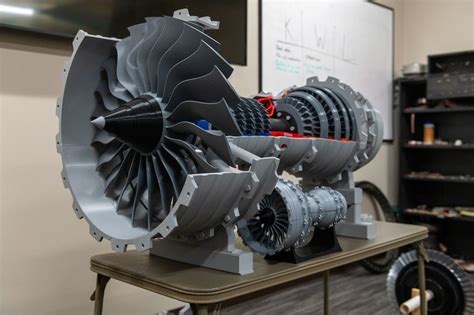
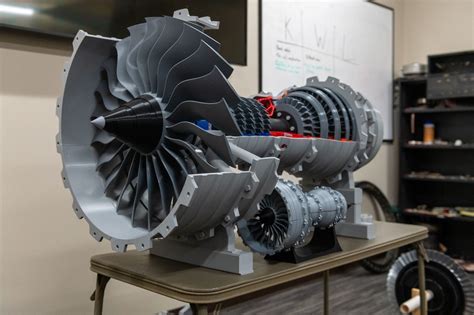

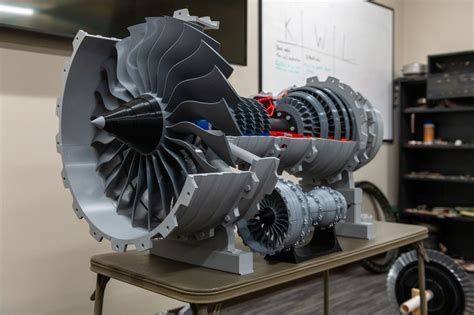
What is 3D printing Lockheed engine tips?
+3D printing Lockheed engine tips refers to the use of additive manufacturing technology to produce customized engine components, such as engine tips, for Lockheed Martin aircraft.
What are the benefits of 3D printing Lockheed engine tips?
+The benefits of 3D printing Lockheed engine tips include improved performance, reduced weight, and increased durability, as well as reduced production time and costs.
What are the challenges associated with 3D printing Lockheed engine tips?
+The challenges associated with 3D printing Lockheed engine tips include the high cost of equipment and materials, limited material availability, and regulatory framework.
In conclusion, the world of 3D printing Lockheed engine tips is rapidly evolving, with ongoing research and development aimed at improving the performance, efficiency, and affordability of this technology. As the aerospace industry continues to push the boundaries of innovation, the use of 3D printing is likely to play an increasingly important role in the production of engine components, enabling the creation of more complex geometries, customized shapes, and advanced materials. We invite you to share your thoughts and experiences with 3D printing Lockheed engine tips, and to explore the many resources and references available on this topic. Whether you are an industry professional, a researcher, or simply an enthusiast, we hope that this article has provided valuable insights and information on the exciting world of 3D printing Lockheed engine tips.